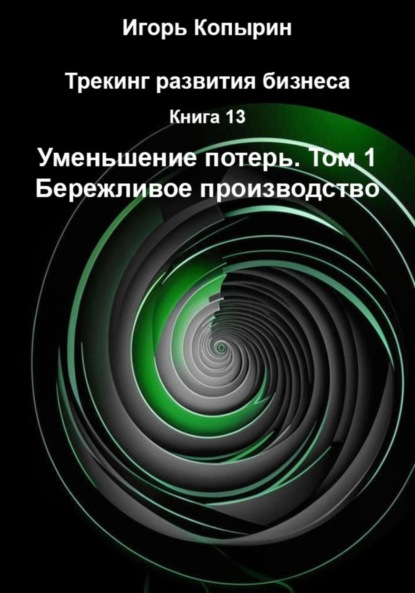
Полная версия:
Книга 13. Уменьшение потерь. Том 1. Бережливое производство
Участие всех сотрудников: Принцип кайзен подчеркивает, что улучшения могут исходить не только от высшего руководства, но и от всех сотрудников на различных уровнях. Каждый работник, независимо от его роли, обладает ценными знаниями, которые могут быть использованы для улучшения процессов.
Долгосрочное видение: Хотя кайзен предполагает внимание к ежедневным улучшениям, он также ориентирован на долгосрочные цели. Важно, чтобы компания могла увидеть перспективы роста и развития, а не только искать краткосрочные выгоды.
Как реализовать кайзен в организации
Реализация кайзен начинается с формирования правильной культуры на всех уровнях компании. Необходимо, чтобы каждый сотрудник, от оператора до менеджера, понимал свою роль в процессе улучшения и активно участвовал в нем. Этот процесс требует времени, терпения и системного подхода, но результаты стоят усилий.
Постановка целей: Четкие и конкретные цели – это основа для работы по кайзену. Они могут быть направлены на улучшение качества, сокращение времени выполнения задач, снижение затрат или оптимизацию рабочих процессов. Каждая цель должна быть измеримой и достижимой.
Обучение и вовлеченность сотрудников: Важнейший шаг – это обучение сотрудников принципам кайзен и вовлечение их в процесс улучшения. Чем больше людей понимают важность кайзен и осознают свою ответственность за улучшения, тем быстрее и эффективнее будет происходить развитие.
Внедрение инструментов кайзен: В рамках кайзен используются различные инструменты и методы для повышения эффективности. Некоторые из них включают в себя:
Карта потока создания ценности (Value Stream Mapping): помогает анализировать потоки материалов и информации на всех этапах производства, выявляя узкие места и потери.
5S: это система организации рабочего пространства, которая включает сортировку, систематизацию, чистоту, стандартизацию и соблюдение дисциплины.
Кайзен-мероприятия: это короткие, интенсивные проекты, в рамках которых группа сотрудников работает над решением конкретной проблемы или улучшением процесса.
Обратная связь и улучшение процесса: Важной частью кайзен является регулярная оценка достигнутых результатов и анализ того, что было сделано. Сбор обратной связи и использование полученных данных для дальнейших улучшений позволяет сохранять динамику изменений.
Примеры успешных внедрений кайзен
Одним из ярких примеров успешного применения кайзен является японская компания Toyota. Ее подход к бережливому производству и кайзен стал образцом для многих мировых компаний. В Toyota каждая команда работает над небольшими улучшениями, которые со временем приводят к значительным результатам. Успех этой системы заключается в том, что компания не ожидает мгновенных революционных изменений, а делает акцент на постепенные улучшения.
Другим примером может служить компания Intel, которая внедрила философию кайзен в своих производственных процессах. В результате, несмотря на высокую конкурентность и технологические вызовы, компания смогла сохранить свою лидерскую позицию благодаря постоянному совершенствованию своих производственных процессов и увеличению производительности.
Преимущества кайзен для организации
Устранение потерь и повышение производительности: Кайзен позволяет минимизировать потери на каждом этапе производства, что способствует улучшению производительности и снижению затрат.
Улучшение качества: Постоянные улучшения позволяют уменьшить количество дефектов и повысить качество продукции, что в свою очередь повышает удовлетворенность клиентов.
Мотивация и вовлеченность сотрудников: Когда сотрудники видят, что их предложения ценятся и приводят к реальным улучшениям, это повышает их мотивацию и вовлеченность в процесс.
Гибкость и адаптивность: Организации, применяющие кайзен, становятся более гибкими и способными быстро адаптироваться к изменениям в рыночных условиях или внутренней среде.
3.1 : Карта потока создания ценности (Value Stream Mapping)
Карта потока создания ценности (Value Stream Mapping, VSM) – это визуальный инструмент Lean-методологии, который помогает выявить потери в процессах и оптимизировать поток ценности от сырья до готового продукта. Создание и внедрение VSM включает пять этапов: подготовка, анализ текущего состояния, проектирование будущего состояния, разработка плана реализации и контроль результатов.
Что такое Карта потока создания ценности (VSM)?
Определение: VSM – это схема или диаграмма, которая отображает шаги процесса, информацию и потоки материалов, необходимых для создания продукта или услуги.
Цель: Обнаружение и устранение неэффективностей (потерь), улучшение времени выполнения (lead time) и качества.
Ключевые элементы:
Поток материалов (материалы, сырье, полуфабрикаты).
Поток информации (инструкции, заказы, данные о производстве).
Время цикла, время простоя, коэффициенты дефектов и другие метрики.
Как создать Карта потока создания ценности?
1. Подготовка: Определение фокуса
Команда: Создайте межфункциональную команду из участников производства, логистики, ИТ и управления.
Цель: Определите, что именно вы хотите улучшить (например, время выполнения заказа или снижение дефектов).
Границы процесса: Установите начальную и конечную точки анализа (например, от заказа до отгрузки).
2. Сбор данных: Анализ текущего состояния
Наблюдение на месте: Пройдите процесс "вживую" (принцип Gemba) и соберите данные о каждом шаге.
Ключевые параметры:
Время цикла (Cycle Time, CT).
Время выполнения (Lead Time, LT).
Процент дефектов.
Запасы (WIP, work in progress).
Рисование карты текущего состояния: Используйте условные обозначения для отображения каждого этапа, включая потоки материалов и информации.
3. Проектирование будущего состояния
Устраните выявленные потери: Уберите лишние шаги, уменьшите запасы, улучшите балансировку операций.
Интегрируйте Lean-инструменты:
Kanban для управления потоками.
Just-in-Time (точно в срок) для минимизации запасов.
Poka-Yoke (защита от ошибок) для предотвращения дефектов.
Постройте "идеальную" карту будущего состояния.
4. План реализации
Разделите внедрение на этапы: Определите краткосрочные (quick wins) и долгосрочные цели.
Назначьте ответственных за каждый этап.
Установите четкие метрики оценки прогресса (KPI).
5. Контроль и адаптация
Проводите регулярные встречи команды для анализа прогресса.
Используйте визуальные доски или софт (например, Miro, Lucidchart или специализированные Lean-системы) для отслеживания изменений.
Постоянно совершенствуйте карту: Lean – это культура непрерывного улучшения.
Как внедрить VSM на производстве?
Обучение персонала:
Проведите тренинги для сотрудников, чтобы они понимали цель и принципы VSM.
Вовлеките их в процесс, чтобы они видели личную ценность изменений.
Пилотный проект:
Начните с одного участка или процесса, чтобы минимизировать риски.
Получите раннюю обратную связь, чтобы корректировать подход.
Стандартизация и масштабирование:
После успешного пилотного внедрения создайте стандарты работы.
Распространите методику на другие подразделения, используя успешный кейс как пример.
Пример использования
На одном из крупных заводов автомобилестроения внедрение VSM позволило сократить время цикла производства двигателя с 15 дней до 8 за счет:
Уменьшения промежуточных складов.
Внедрения системы Kanban между участками.
Ускорения процесса передачи информации о заказах.
VSM – мощный инструмент, который дает видимость "скрытых" проблем. Успех его внедрения зависит от вовлеченности всей команды и ориентации на долгосрочные улучшения.
Глава 4: Создание потока (Flow)
Создание потока (Flow) в бережливом производстве – это процесс организации последовательного и бесперебойного движения материалов, информации и продуктов через все этапы создания ценности. Основная цель – устранение задержек, уменьшение времени выполнения (Lead Time) и оптимизация каждого шага в процессе. Для создания потока применяются такие принципы, как устранение потерь, выравнивание работы (Heijunka) и визуализация.
Что такое "Создание потока"?
Определение: Поток – это непрерывное движение продукта или услуги через процесс, от сырья до готового изделия, без задержек, простоев или избыточных операций.
Цель: Ускорение времени выполнения, снижение издержек и улучшение качества продукции.
Основной принцип: Оптимизация каждого шага процесса для создания максимальной ценности для клиента без ненужных затрат.
Принципы создания потока
Фокус на ценности для клиента: Каждое действие должно приносить ценность клиенту. Если шаг не добавляет ценности, он подлежит устранению.
Устранение потерь (Muda): Идентификация и устранение 7 видов потерь (перепроизводство, запасы, ожидание, ненужные перемещения, избыточная обработка, дефекты и неэффективная логистика).
Выравнивание загрузки (Heijunka): Сглаживание вариаций в объемах и типах производимой продукции для стабильного потока.
Минимизация незавершенного производства (WIP): Создание систем, которые позволяют минимизировать запасы на всех этапах.
Такт времени (Takt Time): Установление ритма производства, который синхронизирован с потребностями клиента.
Как создать поток?
1. Анализ текущего состояния
Постройте Карту потока создания ценности (Value Stream Map).
Определите все этапы процесса, где возникают задержки или потери.
Измерьте ключевые параметры: время цикла (Cycle Time), время выполнения (Lead Time), уровень запасов и другие.
2. Элиминируйте разрывы в потоке
Уберите ненужные этапы или перемещения.
Сократите время ожидания между процессами.
Оптимизируйте транспортировку и логистику.
3. Выравнивайте процесс
Убедитесь, что каждый этап процесса работает с одинаковой скоростью, избегая узких мест.
Используйте такие инструменты, как:
Heijunka для равномерного распределения нагрузки.
Система вытягивания (Pull System) для обеспечения выполнения работы по запросу.
4. Создайте стандартизированные рабочие процедуры
Определите лучшие методы выполнения задач.
Задокументируйте их в виде стандартов, чтобы все сотрудники следовали единому процессу.
5. Визуализируйте поток
Используйте визуальные инструменты, такие как:
Kanban-доски.
Линии потоков и указатели на полу.
Информационные табло с метриками производительности.
6. Проведите пилотный запуск
Начните с одного участка или процесса для тестирования изменений.
Получите обратную связь от команды и улучшите систему до масштабного внедрения.
Преимущества создания потока
Сокращение времени выполнения: Продукт быстрее доходит до клиента.
Снижение затрат: Устранение потерь уменьшает ресурсы, затрачиваемые на создание продукта.
Повышение качества: Последовательность в процессах снижает риск ошибок и дефектов.
Улучшение гибкости: Быстрая реакция на изменения спроса.
Повышение вовлеченности сотрудников: Понятные процессы мотивируют сотрудников и делают их работу эффективнее.
Как внедрить поток в производстве?
Обучение команды:
Объясните концепции потока и его значение.
Привлеките сотрудников к анализу и улучшению процессов.
Устраните узкие места:
Выявите участки с наиболее длинным временем выполнения и начните оптимизацию с них.
Примените Lean-инструменты:
Kanban, чтобы обеспечить управление запасами.
SMED (Быстрая переналадка), чтобы сократить время настройки оборудования.
5S для упрощения и стандартизации рабочих мест.
Регулярно анализируйте результаты:
Внедряйте культуру постоянного улучшения (Kaizen).
Отслеживайте метрики производительности и корректируйте процесс.
Пример создания потока
На производственной линии бытовой техники оптимизация потока позволила сократить время производства одного устройства с 10 дней до 3 дней. Это было достигнуто за счет:
Устранения избыточных перемещений между цехами.
Внедрения Kanban для управления запасами.
Сокращения времени наладки станков с 1 часа до 20 минут с помощью SMED.
Создание потока – это основа бережливого производства, которая делает процесс производства быстрее, дешевле и качественнее. Внедрение требует вовлеченности команды, системного подхода и регулярного контроля за результатами.
Инструменты для улучшения потока: Воронки, карты потока и другие методы визуализации и улучшения потоков
Одним из самых важных аспектов бережливого производства является улучшение потока. Эффективный поток позволяет сократить время цикла, повысить производительность и уменьшить затраты. Однако для того, чтобы понять, как улучшить поток, нужно сначала визуализировать его, выявить узкие места и источники потерь. В этой главе мы рассмотрим инструменты, которые помогают на практике организовать и улучшить потоки в рамках бережливого производства.
1. Воронки
Воронка – это инструмент, который используется для отображения стадий процесса и количества единиц, которые проходят через каждую из них. Визуализация с помощью воронки помогает выявить узкие места, где происходит задержка, и понять, как различные этапы процесса взаимодействуют друг с другом.
Воронка обычно используется для того, чтобы отследить, как материалы или работы перемещаются по различным этапам производственного процесса. На верхней части воронки можно разместить начальную точку – например, количество заказов или материалов, которые поступили в систему, а на нижней – конечный результат, такой как завершенные работы или отгруженные товары. На каждом промежуточном этапе воронки отображается количество единиц, которые были обработаны, что позволяет выявить места с наибольшими задержками.
Как использовать воронки:
Для анализа каждого этапа процесса.
Для выявления этапов, на которых наблюдаются заторы или значительные потери времени.
Для оптимизации работы на стадии с минимизацией потерь.
2. Карты потока
Карты потока (или карты потока стоимости) – это диаграммы, на которых отображаются все шаги процесса, начиная от получения сырья и заканчивая доставкой готовой продукции потребителю. Карты потока используются для того, чтобы детально понять, как каждый этап в цепочке добавляет или забирает ценность и время, позволяя выявить, где могут происходить потери.
Карты потока обычно включают:
Процесс – шаги, которые выполняются на каждом этапе.
Время – время, затраченное на каждый шаг.
Запасы – количество материалов или товаров, находящихся в процессе.
Перерывы и задержки – этапы, на которых происходят простои или неэффективность.
Каждый шаг, который не добавляет ценности, рассматривается как потери. Визуализация всего процесса помогает понять, на каких этапах можно снизить затраты времени, и где можно исключить излишние действия.
Как использовать карты потока:
Для оценки стоимости и времени на каждом шаге процесса.
Для поиска этапов с неэффективным использованием ресурсов.
Для определения возможностей для улучшения и устранения потерь.
3. Диаграмма потока
Диаграмма потока – это еще один способ визуализации производственного процесса. В отличие от карты потока, диаграмма потока обычно используется для отображения более линейных и менее комплексных процессов. На диаграмме шаги процесса изображаются в виде блоков, соединенных стрелками, которые указывают направление движения материала или работы.
Диаграммы потока удобны для анализа простых процессов или отдельных операций, где важно понимать последовательность действий, а также возможность возникновения задержек или ошибок.
Как использовать диаграмму потока:
Для улучшения простых, повторяющихся процессов.
Для анализа последовательности действий в процессе.
Для выявления возможных точек сбоя или неэффективных взаимодействий.
4. Методики анализа работы (Workload Balance)
Методика анализа работы позволяет оценить, насколько сбалансированно распределены рабочие нагрузки между различными участками процесса. Это особенно важно в рамках бережливого производства, так как балансировка позволяет оптимизировать потоки и избежать перегрузок на отдельных участках.
Конец ознакомительного фрагмента.
Текст предоставлен ООО «Литрес».
Прочитайте эту книгу целиком, купив полную легальную версию на Литрес.
Безопасно оплатить книгу можно банковской картой Visa, MasterCard, Maestro, со счета мобильного телефона, с платежного терминала, в салоне МТС или Связной, через PayPal, WebMoney, Яндекс.Деньги, QIWI Кошелек, бонусными картами или другим удобным Вам способом.
Вы ознакомились с фрагментом книги.
Для бесплатного чтения открыта только часть текста.
Приобретайте полный текст книги у нашего партнера:
Полная версия книги
Всего 10 форматов