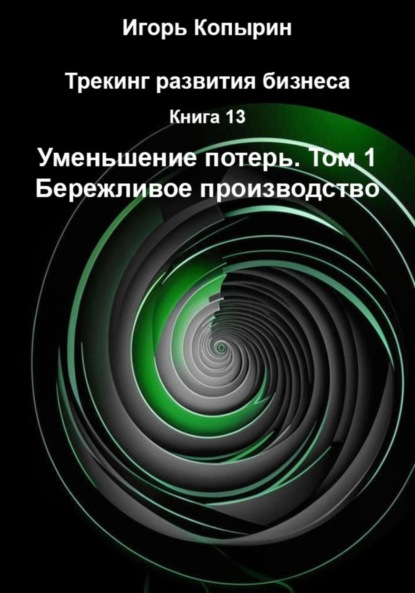
Полная версия:
Книга 13. Уменьшение потерь. Том 1. Бережливое производство

Игорь Копырин
Книга 13. Уменьшение потерь. Том 1. Бережливое производство
Введение
В современном мире высокой конкуренции и нестабильной экономической ситуации эффективное управление производственными процессами становится ключевым фактором успеха любого предприятия. Данная книга представляет собой практическое руководство по внедрению принципов бережливого производства – философии, доказавшей свою эффективность в повышении производительности и минимизации потерь.
Бережливое производство – это не просто набор инструментов, а целостная система мышления, направленная на создание максимальной ценности для клиента при минимальных затратах ресурсов. В этом издании мы подробно рассмотрим основные типы потерь, методы их выявления и ликвидации, а также практические шаги по трансформации производственных процессов.
Читатель найдет в книге:
Пошаговые инструкции по внедрению инструментов бережливого производства
Реальные кейсы успешной оптимизации процессов
Практические упражнения для самостоятельной работы
Шаблоны документов и чек-листы для оценки текущего состояния
Рекомендации по преодолению сопротивления изменениям
Книга предназначена для руководителей производственных предприятий, менеджеров по развитию, специалистов по улучшению процессов, а также всех, кто заинтересован в повышении эффективности бизнеса. Особое внимание уделяется практическим аспектам внедрения изменений и работе с персоналом.
Я уверен, что системный подход к внедрению бережливого производства, описанный в данной книге, поможет читателям достичь значительного улучшения показателей своего предприятия и создать устойчивую систему постоянных улучшений.
Глава 1: Введение в бережливое производство: История и философия
Бережливое производство, или Lean production, представляет собой концепцию управления производственными процессами, направленную на максимизацию ценности для клиента при минимизации всех видов потерь. Это не просто методология, а целая философия, которая охватывает все аспекты деятельности компании, от разработки продукта до его доставки конечному потребителю. Основной акцент в бережливом производстве делается на непрерывные улучшения, максимальную эффективность и устранение всего, что не добавляет ценности.
История бережливого производства
История бережливого производства начинается в Японии в 1950-х годах, когда компания Toyota под руководством авто конструктора Киичиро Тоёды начала разрабатывать свою уникальную производственную систему, известную позже как Toyota Production System (TPS). Главной задачей было создать систему, способную производить автомобили высокого качества при минимальных затратах и максимальной гибкости.
В отличие от традиционных западных методов массового производства, где акцент делался на увеличение объемов и ресурсов, японские инженеры предложили концепцию, где важнейшими были скорость и качество при минимуме ресурсов. Это позволило компании Toyota добиться значительного преимущества на международном рынке.
Одним из важнейших шагов в развитии этой системы стало внедрение принципа «Just in Time» (JIT), что означает «точно вовремя». Этот подход предполагает, что товары и материалы поступают на производство только в нужный момент, без излишних запасов. Такой подход позволил значительно снизить затраты на хранение и снизить риски, связанные с неэффективным использованием ресурсов.
В то же время компания Toyota разработала принципы управления качеством, ориентированные на вовлечение каждого сотрудника в процесс улучшения, и внедрила методы визуализации данных, такие как канбан, для управления потоками материалов и деталей.
Принципы, разработанные в рамках Toyota Production System, позже стали основой для бережливого производства. В 1990-х годах, благодаря труду исследователей, таких как Джеймс Уомак и Даниэль Джонс, эти идеи были систематизированы и изложены в книге «The Machine That Changed the World». В этой книге был подробно описан опыт Toyota и предложены рекомендации по внедрению бережливого производства в различные отрасли.
Философия бережливого производства
В основе философии бережливого производства лежит идея создания ценности для потребителя при минимизации потерь. Это означает, что каждый процесс должен быть нацелен не на производство «избыточного» продукта, а на создание того, что будет полезно конечному потребителю.
Основные принципы философии Lean включают:
Создание ценности: Вся работа и усилия должны быть направлены на создание ценности для клиента. Это требует четкого понимания потребностей и предпочтений конечного пользователя.
Устранение потерь: Потери могут быть разных видов, включая излишние запасы, ненужные процессы, лишнее время ожидания и прочие виды неэффективности. Бережливое производство активно ищет способы их устранения.
Непрерывное улучшение (кайзен): это культура, которая мотивирует всех сотрудников постоянно искать способы улучшить процессы, уменьшить затраты и повысить качество.
Вовлечение всех сотрудников: в отличие от традиционных подходов, где решения принимаются только высшим руководством, в бережливом производстве каждый работник имеет право предлагать идеи по улучшению, потому что они лучше всего знают процессы на своем уровне.
Система «потоков»: Бережливое производство стремится создать максимально плавный и непрерывный поток работы, что позволяет значительно сократить время выполнения процессов и снизить затраты.
Стандартизация процессов: Стандарты помогают обеспечить стабильность и высокое качество, а также легкость в обучении новых сотрудников.
Бережливое производство – это не только набор инструментов и методик, но и целая культура, которая трансформирует всю организацию. Его философия фокусируется на создании ценности для клиентов через максимальную эффективность и качество на всех уровнях бизнеса.
Преимущества и вызовы
Одним из основных преимуществ бережливого производства является значительное сокращение затрат за счет устранения потерь и повышения эффективности. Это позволяет компаниям не только снижать издержки, но и повышать гибкость, ускоряя процессы и сокращая время от разработки до доставки конечного продукта. Внедрение Lean позволяет также улучшить качество продукции и услуг, повышая удовлетворенность клиентов.
Однако внедрение бережливого производства сопряжено с рядом вызовов. Одним из них является необходимость изменений в корпоративной культуре. Принципы Lean требуют от всех сотрудников активного участия в процессе улучшений, что может столкнуться с сопротивлением, особенно в тех организациях, где существует устоявшийся порядок и привычки. Также внедрение Lean требует значительных усилий на этапе обучения и адаптации.
Вместе с тем, несмотря на эти вызовы, бережливое производство стало основой для многочисленных успешных кейсов в разных отраслях, от автомобильной и электронной промышленности до здравоохранения и образования. Это подтверждает его универсальность и эффективность в решении широкого круга задач.
Глава 2: Основные принципы бережливого производства: Принципы Toyota Production System (TPS) и их применение
Бережливое производство (Lean Manufacturing) – это система управления производственными процессами, целью которой является создание максимальной ценности для потребителей при минимальных затратах ресурсов. Система бережливого производства берет свое начало в Toyota Production System (TPS), разработанной японской компанией Toyota в 1950-е годы, и с тех пор претерпела эволюцию, но основные принципы остались неизменными. В этой главе мы рассмотрим ключевые принципы TPS, их значение и применение в различных сферах бизнеса.
1. Устранение потерь (Muda)
Принцип устранения потерь является основой TPS. Потери (или "муда" в японской терминологии) – это все действия или процессы, которые не добавляют ценности для конечного потребителя. В рамках TPS выделяют семь типов потерь:
Перепроизводство: Излишнее производство, которое превышает реальный спрос.
Ожидание: Время, когда сотрудники, оборудование или материалы простаивают без действия.
Транспортировка: Лишние перемещения материалов и продукции.
Излишняя обработка: Неоправданные процессы, которые не улучшают качество продукта.
Запасы: Избыточные запасы материалов, которые требуют хранения и управления.
Дефекты: Некачественная продукция, требующая переработки или уничтожения.
Неэффективность труда: Нерациональное использование человеческих ресурсов.
Каждый из этих типов потерь должен быть идентифицирован и устранен на всех этапах производственного процесса, чтобы повысить общую эффективность.
2. Создание потока (Flow)
Создание потока – это организация работы так, чтобы производство шло непрерывно, без задержек и простоя. В идеале, весь процесс производства должен быть спроектирован таким образом, чтобы материалы и компоненты двигались от одной операции к другой без лишних остановок или пересадок. Эффективный поток сокращает время цикла, повышает производительность и уменьшает затраты на управление запасами.
Для создания потока важно:
Упрощать и стандартизировать рабочие процессы.
Использовать методы "one-piece flow" (поток одной единицы продукции) для минимизации времени, затрачиваемого на переключение между различными задачами.
Перераспределять ресурсы и оборудование для минимизации времени ожидания и перемещения материалов.
3. Тянущий процесс (Pull)
Принцип "тянущего" производства заключается в том, чтобы производственные процессы начинались только в том случае, если существует реальный спрос на продукцию. В отличие от "толкающего" процесса, при котором производство начинается заранее, без учета потребностей рынка, в тянущем процессе каждая стадия производства "тянет" за собой следующую только тогда, когда предыдущая стадия завершена.
Система канбан, одна из основных составляющих TPS, является примером тянущего процесса. Канбан использует карточки или другие визуальные сигналы для того, чтобы отслеживать потребности на каждом этапе производства. Когда на одном этапе производства требуется больше материалов или компонентов, система канбан сигнализирует об этом, и нужные материалы "тянутся" к следующей стадии.
4. Управление качеством в рамках бережливого производства: Применение принципов качества на каждом этапе
Внедрение и поддержание системы качества являются неотъемлемой частью бережливого производства. Бережливое производство (Lean) и управление качеством не являются противоположностями, наоборот, они идеально дополняют друг друга. Применение принципов качества на каждом этапе производственного процесса позволяет не только повышать производительность, но и сокращать затраты, улучшать общие результаты и повышать удовлетворенность клиентов.
4.1. Качество как основа бережливого производства
В бережливом производстве качество рассматривается не как отдельный аспект, а как ключевая составляющая всех процессов. В отличие от традиционных моделей, где контроль качества часто осуществляется в конце производства, Lean-система фокусируется на поддержании высокого качества на каждом этапе работы, с самого начала. Это обеспечивает снижение дефектов и потерь, а также ускоряет производственные циклы.
Основные принципы бережливого производства, такие как устранение потерь (муда), улучшение потока и стандартизация процессов, напрямую связаны с качеством. В рамках Lean подхода качество строится через вовлеченность всех участников процесса, а не только работников отдела контроля качества. Каждый сотрудник должен быть ответственным за качество своей работы и осознавать его важность для общего успеха компании.
4.2. Принципы управления качеством в Lean
Управление качеством в Lean включает несколько ключевых принципов и методов:
4.2.1. Понять и устранить причины дефектов
Важно не просто обнаружить дефекты, но и понять их коренные причины. Методика "5 почему" (5 Whys) используется для анализа проблем и нахождения корня причины. Это позволяет не только устранить последствия, но и избежать повторных ошибок в будущем. Каждый дефект – это шанс улучшить процесс, и он должен быть воспринят как ценный сигнал.
4.2.2. Контроль на месте (Jidoka)
Jidoka, или "автоматизация с человеческим элементом", предполагает, что любые отклонения от нормы должны быть немедленно зафиксированы и устранены. На каждом рабочем месте должны быть созданы условия для того, чтобы сотрудники могли остановить процесс в случае возникновения проблем, а также оперативно решать возникшие вопросы. Это предотвращает распространение дефектов по всему производству.
4.2.3. Стандартизация процессов
Стандарты играют важную роль в поддержании стабильного качества. Стандартизированные рабочие инструкции и процессы помогают избежать вариативности в работе, снижая риск ошибок и дефектов. Внедрение стандартов помогает поддерживать высокое качество, обеспечивая предсказуемость и эффективность на всех этапах.
4.2.4. Качество на каждом этапе (Built-in Quality)
В отличие от традиционных подходов, где качество часто контролируется на последних этапах, в Lean качество строится на каждом шаге производственного процесса. Это концепция "качества на каждом этапе", или "built-in quality", позволяет минимизировать риски появления дефектов на поздних стадиях и значительно уменьшить затраты на исправление ошибок.
Каждый сотрудник обязан не только выполнять свою работу, но и следить за тем, чтобы её выполнение соответствовало установленным стандартам качества. Это требует постоянной обратной связи и вовлеченности всей команды в процесс улучшений.
4.2.5. Циклы улучшений (Кайзен)
Кайзен, или культура постоянных улучшений, является неотъемлемой частью Lean и не ограничивается только производственными процессами. Это касается всех аспектов деятельности организации, включая управление качеством. Улучшения должны быть небольшими, но постоянными и последовательными. Каждое улучшение качества должно быть результатом совместных усилий команды, что помогает создавать культуру, ориентированную на совершенствование.
4.3. Методы обеспечения качества в Lean
4.3.1. Kanban для управления качеством
Kanban-система используется не только для оптимизации потока материалов, но и для управления качеством. Используя визуальные инструменты, такие как карточки или доски Kanban, можно отслеживать качество на каждом этапе и быстро реагировать на возникающие проблемы. Применение таких систем способствует прозрачности, позволяет всем сотрудникам видеть текущее состояние процессов и вовремя выявлять отклонения от норм.
4.3.2. Обратная связь от клиентов
Клиенты должны быть активно вовлечены в процесс управления качеством. Регулярная обратная связь от клиентов, сбор отзывов и мониторинг удовлетворенности помогают определить области, требующие улучшений, и оперативно устранять недостатки. Это особенно важно в условиях высококонкурентной среды, где удовлетворение потребностей клиентов напрямую влияет на успех компании.
4.3.3. Использование технологий для контроля качества
Системы автоматизации, датчики, а также передовые технологии, такие как искусственный интеллект и машинное обучение, могут быть использованы для мониторинга и контроля качества в реальном времени. Применение этих технологий позволяет не только быстро обнаруживать отклонения, но и предсказать их появление на основе анализа данных, что помогает предотвращать возможные дефекты до их возникновения.
Глава 3: Оценка и устранение потерь (Muda):
Виды потерь в производственном процессе и методы их минимизации
Одной из центральных задач в бережливом производстве является выявление и устранение потерь. Потери – это все те элементы производственного процесса, которые не добавляют ценности для конечного потребителя и, следовательно, должны быть минимизированы или полностью устранены. Идея заключается в том, чтобы сосредоточить усилия на создании максимально эффективного и ценного потока, устраняя все излишества, которые замедляют процесс или увеличивают затраты. В этой главе мы подробно рассмотрим различные виды потерь, которые встречаются в производственном процессе, и методы их минимизации.
1. Типы потерь в производственном процессе
В рамках бережливого производства выделяется семь основных типов потерь, которые имеют прямое влияние на эффективность и стоимость производственных процессов. Эти потери были определены в рамках концепции Toyota Production System (TPS), и они служат ориентиром для всех компаний, стремящихся к совершенствованию процессов.
1.1. Перепроизводство
Перепроизводство – это производство большего количества продукции, чем необходимо для удовлетворения потребностей клиента. Это может привести к излишним запасам, которые требуют хранения, а также увеличивают риск устаревания продукции. Перепроизводство также может блокировать ресурсы, которые могут быть использованы для производства другой продукции, более востребованной на рынке.
Методы минимизации:
Использование системы канбан для управления запасами и производства в точном соответствии с потребностями.
Внедрение производственного планирования по заказу вместо прогнозирования, чтобы предотвратить излишки.
Оценка спроса и оптимизация производственных процессов в соответствии с этим спросом.
1.2. Ожидание
Ожидание происходит, когда сотрудники или машины вынуждены тратить время на ожидание материалов, инструментов, информации или другого оборудования. Это потеря времени, которая негативно сказывается на общей производительности.
Методы минимизации:
Оптимизация потоков материалов и информации.
Внедрение точной логистики и гибких рабочих расписаний, чтобы минимизировать время ожидания.
Автоматизация и стандартизация процессов для сокращения времени на настройку и подготовку.
1.3. Транспортировка
Избыточная транспортировка материалов или продукции через большие расстояния без добавления ценности для клиента также является одной из форм потерь. Она требует дополнительного времени, усилий и ресурсов.
Методы минимизации:
Оптимизация расположения рабочих станций и складов.
Использование гибкой логистики и местных поставок, чтобы минимизировать транспортные расходы.
Внедрение автоматических транспортных систем или роботов для ускорения движения материалов.
1.4. Излишняя обработка
Излишняя обработка включает в себя выполнение работы, которая не добавляет ценности для продукта или клиента. Это может быть результатом избыточных операций, более сложных методов, чем требуется, или низкой квалификации сотрудников.
Методы минимизации:
Стандартизация рабочих процессов для устранения ненужных шагов.
Использование шести сигм для улучшения качества и устранения ошибок.
Обучение сотрудников и внедрение кайзен для постоянного улучшения процессов.
1.5. Излишние запасы
Запасы, которые не используются или не могут быть проданы в ближайшем будущем, являются еще одной формой потерь. Они занимают пространство, требуют ресурсов для управления и могут стать устаревшими или поврежденными.
Методы минимизации:
Использование точной логистики и принципа just-in-time (JIT) для минимизации запасов.
Анализ данных и прогнозирование потребностей для поддержания минимального уровня запасов.
Постоянная работа с поставщиками для оптимизации поставок.
1.6. Неэффективная работа сотрудников
Неэффективная работа сотрудников включает в себя как физическое, так и интеллектуальное неиспользование их полного потенциала. Это может быть связано с плохим организационным процессом или неправильной мотивацией.
Методы минимизации:
Обучение и развитие сотрудников для повышения их квалификации.
Улучшение условий работы для снижения усталости и повышения производительности.
Вовлечение сотрудников в процесс постоянных улучшений через кайзен.
1.7. Дефекты и ошибки
Дефекты продукции или ошибок в процессе сборки ведут к дополнительным затратам на исправление, а также ухудшают качество и могут вызвать потерю клиентов.
Методы минимизации:
Внедрение системы контроля качества на каждом этапе производственного процесса.
Использование пяти почему и диаграмм Исикавы для анализа и устранения причин дефектов.
Применение подходов шести сигм для улучшения процессов и предотвращения ошибок.
2. Методы и инструменты для минимизации потерь
Для эффективного устранения потерь компании применяют различные методы и инструменты. Некоторые из них включают:
2.1. Метод 5S
Метод 5S (сортировка, систематизация, содержание, стандартизация, совершенствование) помогает организовать рабочие места и процессы так, чтобы минимизировать потери времени и материалов. Это включает в себя создание чистых и упорядоченных рабочих мест, где все необходимое находится на своем месте.
2.2. Кайзен
Кайзен – это подход к постоянному улучшению процессов. Он включает в себя регулярное анализирование и совершенствование каждого этапа производства, а также вовлечение всех сотрудников в этот процесс.
2.3. Анализ потоков добавленной стоимости (VSM)
VSM помогает визуализировать все этапы процесса, выявить потери и установить улучшения для устранения неэффективности. Этот инструмент позволяет точно определить, где происходят потери и как их можно сократить.
2.4. Теория ограничений
Теория ограничений фокусируется на выявлении и устранении узких мест в производственном процессе, которые ограничивают общий поток и производительность.
3: Кайзен: Постоянные улучшения как ключевая концепция бережливого производства
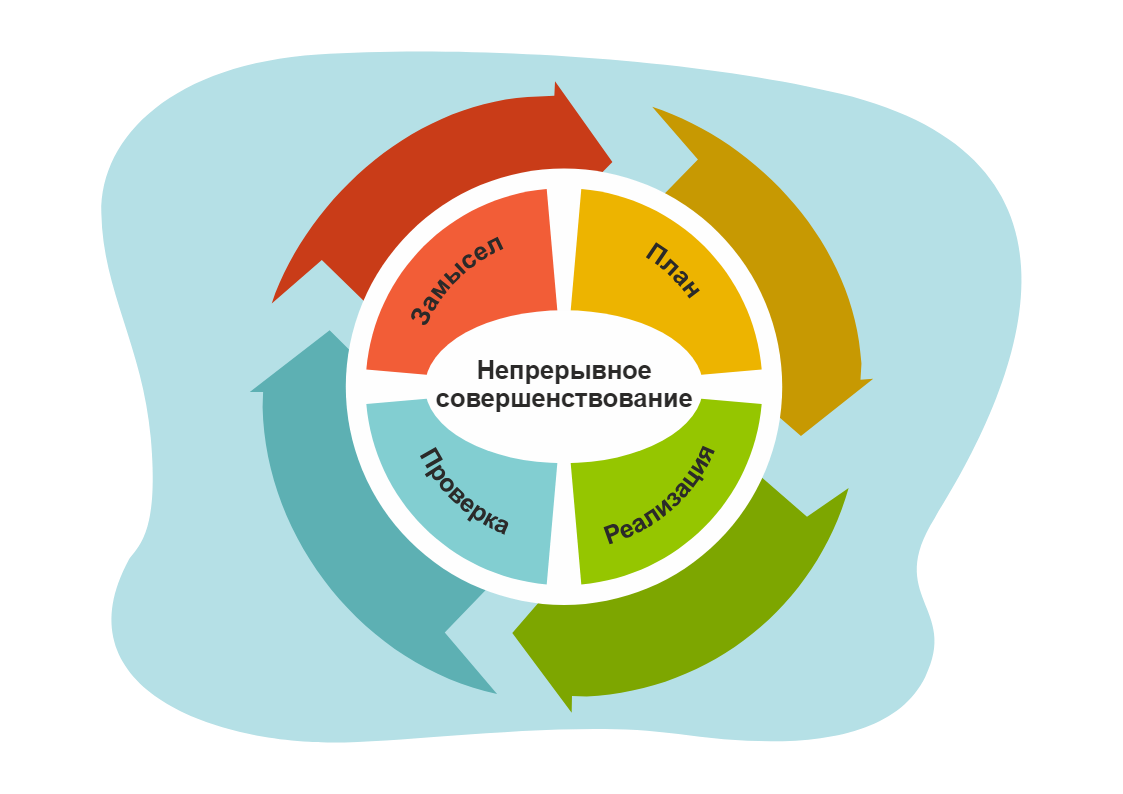
Одним из наиболее важных и эффективных аспектов бережливого производства является философия кайзен, что в переводе с японского означает «постоянные улучшения». Этот принцип лежит в основе системы Toyota Production System (TPS) и является неотъемлемой частью подхода, ориентированного на минимизацию потерь и повышение ценности для клиента. Кайзен – это не просто методика, а философия, которая предполагает непрерывное совершенствование всех процессов, начиная от управления и заканчивая техническим обслуживанием оборудования.
Принципы кайзен
Непрерывное улучшение: Кайзен утверждает, что улучшения не должны быть разовыми или эпизодическими. Это процесс, который происходит каждый день, постоянно и на всех уровнях организации. Суть кайзен в том, чтобы создавать культуру, в которой сотрудники на всех уровнях вносят свой вклад в улучшение рабочих процессов. В этом контексте важны даже малые изменения, поскольку они складываются в значительные улучшения со временем.
Минимизация потерь: Кайзен направлен на устранение всех видов потерь (муда) – будь то время, ресурсы, излишние движения или неоптимальные процессы. Каждое улучшение стремится устранить неэффективности и оптимизировать рабочие процессы.