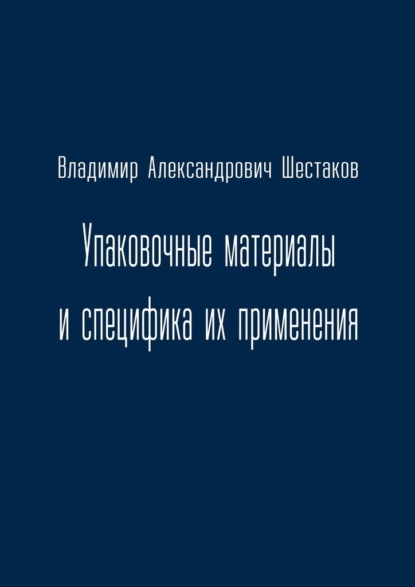
Полная версия:
Упаковочные материалы и специфика их применения
Процесс целенаправленной нагартовки с помощью специальных операций происходит под воздействием внешних сил. Существует два метода образования нагартовки:
Дробеструйный способ. Данный процесс организован с использованием дроби диаметром до 4 мм, которая выбрасывается на поверхность детали с огромной скоростью.
Центробежно-шариковый способ. Принцип действия метода выражается в использовании вращающегося обода, в гнездах которого расположены специальные шарики. При вращении в результате центробежной силы шарики отбрасываются в крайнее положение, нанося удар по обрабатываемой детали.6
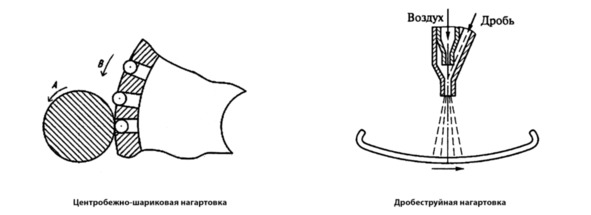
Металлическая лента может иметь несколько типов защитного покрытия. Среди них: цинк, лак, парафин, воск.
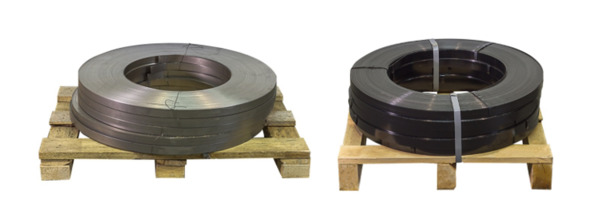
Слева лента без покрытия, справа – с покрытием лак + воск
Стальная металлическая лента применяется в симбиозе с ручным упаковочным инструментом: МУЛ-17, М4К-10 (Украина), китайскими A333, GD-35 (Китай) или европейскими аналогами. Данный инструмент не требует скоб для крепления ленты, лента просекается, образуя надежное крепкое соединение «ласточкин хвост».
Стальные упаковочные ленты 30мм скрепляют при помощи металлических скоб специальным инструментом: ручным механическим инструментом (натяжитель и клипсатор) или пневматическим инструментом 2в 1.
По точности изготовления лента бывает с:
· Нормальной точностью по толщине и ширине (маркируется без обозначения)
· Повышенной точностью по толщине (Т)
· Повышенной точностью по ширине (Ш)
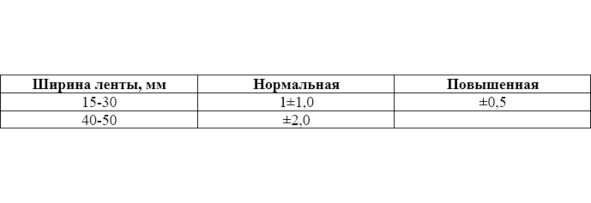
Таблица 4. Точность изготовления стальной ленты
Человеку, впервые увидевшему обозначение стальной ленты нужных параметров, оно не скажет абсолютно ничего. Поэтому в разговоре с менеджером зачастую просто повторяется увиденное обозначение. Часто случается, что нужная лента обозначена неправильно или с лишними дополнениями. Так же часто обращаются по ленте другого ГОСТа.7
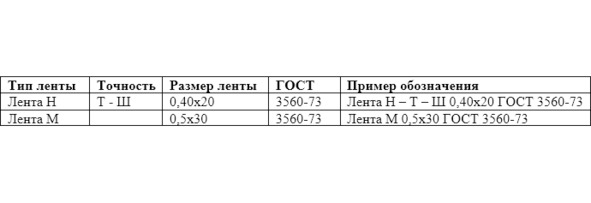
Таблица 5. Параметры и обозначения
Каждый типоразмер ленты предусматривает определенную плотность, выраженную в количестве гр\метр или кг\кольцо.
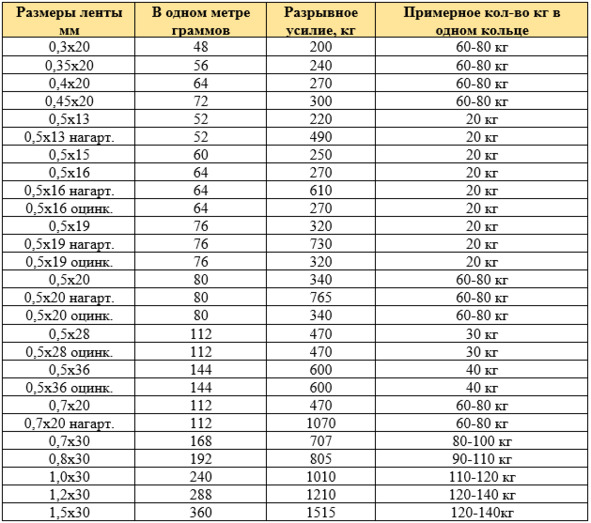
Таблица 6. Разрывные нагрузки для стальной ленты
Также стальная лента разделяется на однорядную и многорядную. Это важно учитывать при выборе размотчика, т.к. многорядная по ширине не влезет в однорядный диспенсер.
Существует формула для расчета количества погонных метров намотки стальной ленты в одном ролике:
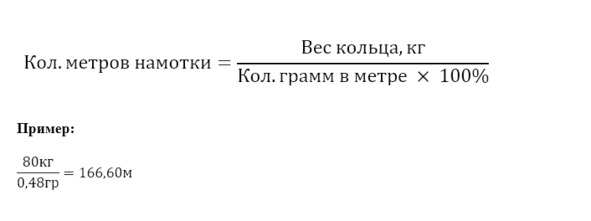

Пример ролика с многорядной намоткой
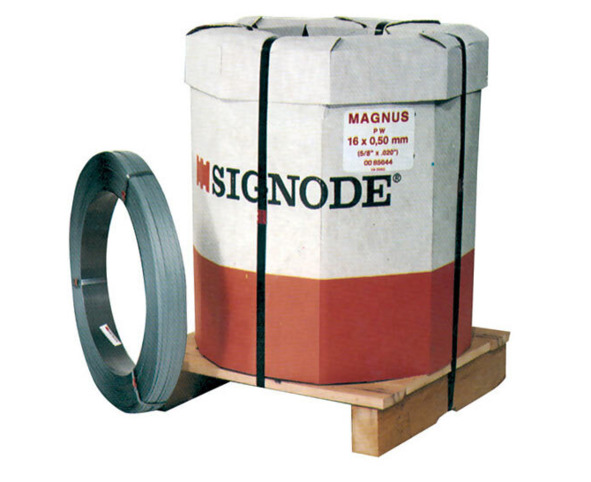
Упаковка многорядной ленты Signode
Примечание: стальная лента встречается в однорядной и многорядной намотке. Ролик ленты достаточно тяжелый, в среднем 20—80кг, поэтому при работе с данной лентой рекомендуется использовать тележку-размотчик.
1.5.2. Разница между холоднокатанной и горячекатанной стальной лентой
На сегодняшний день в мире существует два основных вида сплавов углерода с железом – холоднокатаная и горячекатаная сталь. Все остальные модификации входят в два этих понятия. Технологические различия наступают на стадии окончательной обработки и раскатки металла в листы.

Горячекатаный лист
Горячекатаная и холоднокатаная стали отличаются тем, что первый вид получает свою окончательную форму в раскаленном виде, а второй обрабатывается холодным. Дело в том, что горячая сталь хорошо поддается сгибанию, держит полученную форму и не рвется под давлением. Поэтому можно производить манипуляции с деталями любой толщины. Холодный сплав склонен к сопротивлению любым видам деформаций, плохо держит установленную форму и при избыточном воздействии может порваться. Так что таким способом получают только листы небольшой толщины. Это обуславливает сферу применения данного вида стали, который используют для изготовления корпусов различных устройств, строительных и обшивочных материалов, кузовов для транспортных средств. Изначально изготавливается рулонная сталь методом горячей прокатки. Для горячекатаных листов используется марка стали 3 и сталь 09Г2С. А для холоднокатаных листов 08ПС. Дальше горячекатаный лист раскраивают на ленту или листы небольшого размера. Холоднокатаные листы проходят более длинный путь обработки: листы подвергаются травлению, и только после этого передаются на станы холодной прокатки.
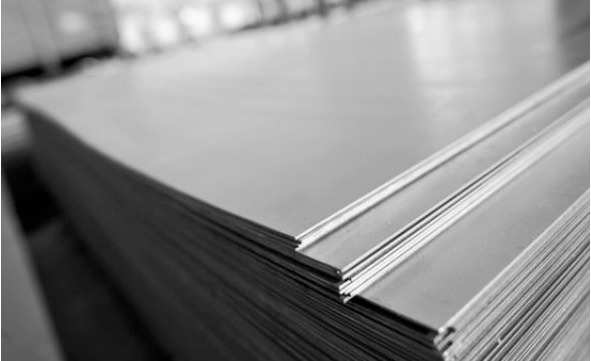
Холодный прокат
Именно поэтому толщина холоднокатаного стального листа не превышает 1см, но поверхность листа получается значительно качественнее (ровнее).
1.6. PES-лента, кордстрап
CordStrap или кордовая лента представляет собой ленту из мягкого полиэстера, она производится путем соединения прочнейшего полиэфирного волокна. Обладая более высокой эластичностью она является во многих случаях наилучшим решением для упаковки тяжелых, объемных грузов со сложной геометрией. Кордовая лента может служить хорошей альтернативой не только полимерным лентам, но и металлическим аналогам. Применение этой ленты обеспечивает высокую прочность фиксации обвязанного груза, не уступающую прочности стальной ленте, при этом мягкость ленты препятствуют разрушению и деформации углов.
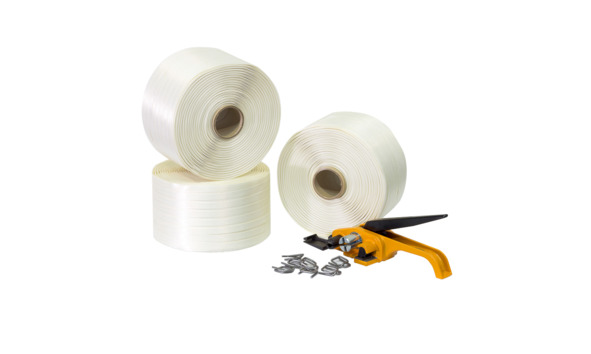
Ролики кордстрапа, проволочные пряжки и натяжитель с упором
Лента содержит волокна из силиконизированного полипропилена или полиэфирных нитей (стекловолокна из полиэстера), пропитанные специальными клеями, чтобы придать им высокие разрывные усилия. Наиболее распространенные волокна для обвязочной ленты включают натуральный и синтетический (модифицированный) каучук. Эти волокна и композитные составы придают ленте прочность, которая может превзойти даже ПЭТ ленты и стальные. Однако области применения кордстрапа крайне ограничены, именно поэтому лента не получила настолько широкого распространения в сфере упаковки, как полимерные аналоги.
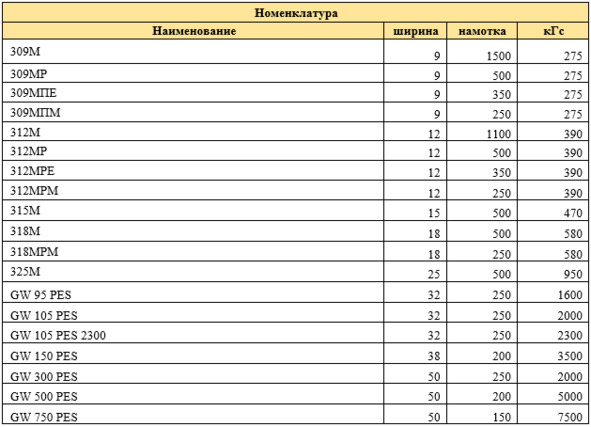
Таблица 7. Ходовые типоразмеры ленты кордстрап
Раздел №2. Процесс производства стреппинг-лент
2.1. Типы полимерного сырья для стреппинг-лент
Полимерные ленты производятся методом экструзии. Экструзия, наряду с литьем пластмасс под давлением, является одним из самых популярных методов изготовления пластмассовых изделий.
Экструзия – это технологический процесс получения из полимерных материалов изделий неограниченной длины путем выдавливания (от англ. extrusion – выталкивание, выдавливание) расплава полимерного через формующую головку (фильеру) нужного профиля.
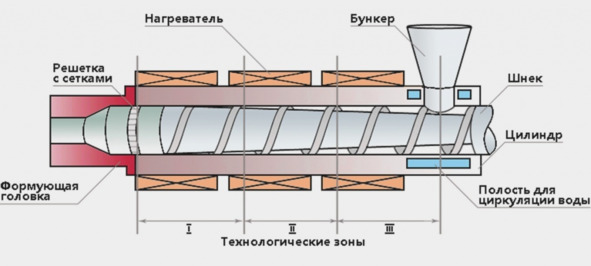
Схема экструдера
Для производства ПП-лент используются полипропиленовые гранулы. В процессе они проходят этапы экструзии, охлаждения, вытяжки и стабилизации.
Лента бывает двух видов:
Первичная. Изготавливается из нового сырья, поэтому стоимость такого материала выше. Цвет – более светлый. Качество производимой ленты на порядок выше.
Вторичная. Производится из первичной ленты, не прошедшей контроль качества. Материал проходит через экструдер и смешивается с новым сырьем. Имеет характерный серый цвет, но не отличается по эксплуатационным характеристикам от первичной. Вторичным сырьём так же может быть переработка различных полимерных изделий (плёнки, бутылки и проч.), подходящих по химическому составу для изготовления лент.
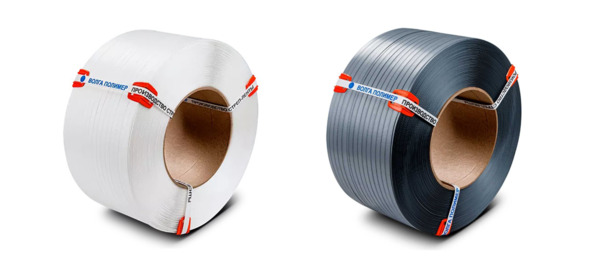
Лента из первичного сырья (слева) и из вторичного
Лента из первичного сырья дороже в производстве, но отвечает самым высоким стандартам качества, и применяется для использования с автоматическими арочными машинами и на конвейерных линиях.
Лента из вторичного сырья является более дешевой, и применяется для упаковки на скобу, пряжку, и с помощью электроинструмента и полуавтоматических столов.
Разрывные нагрузки у обеих лент одинаковые, как заявлено по ТУ. Однако необходимо учитывать, что качество вторичного сырья может быть нестабильным от партии к партии, что скажется на надежности готовой продукции.
2.2. Этапы производства полимерной ленты
1-й этап. Настройка экструдера
Перед загрузкой сырья необходимо настроить параметры работы экструдера. Экструдер осуществляет процесс переработки полимерного сырья в однородный расплав и придаёт ему форму путём продавливания через экструзионную головку и специальное калибрующее устройство.
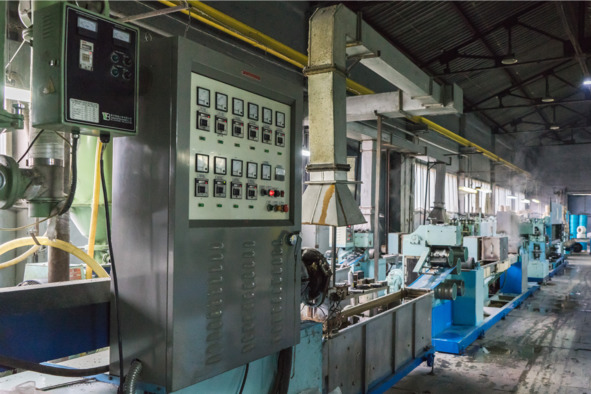
Пульт управления линией
2-й этап. Загрузка полимерного сырья в бункер экструдера
Полимерное сырье поступает на предприятие чаще всего в виде гранул ПП разных марок, например 01030. Затем в необходимых количествах сырье загружается в бункер экструдера.
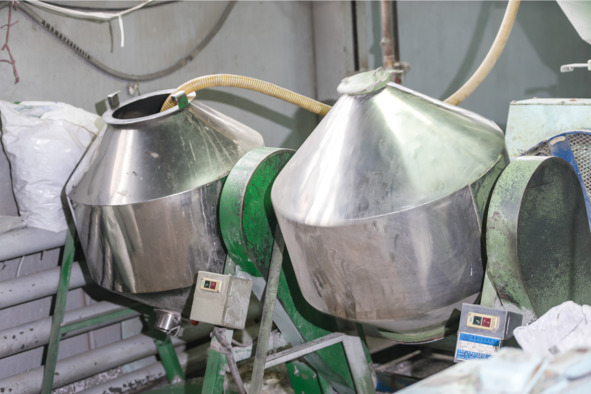
Бункеры с сырьём
3-й этап. Формование
Из бункера, минуя горловину загрузочной воронки, сырьё попадает в загрузочную зону шнека, а затем транспортируется по цилиндру пластикации. От сдавливания, перемешивания и контакта с нагретым цилиндром и шнеком полимерное сырьё расплавляется и превращается в однородную массу – расплав. После чего, на выходе из формующей головки (головка снабжена адаптером, с помощью которого задаются основные настройки), получается полимерная лента, еще далекая от своего конечного состояния.
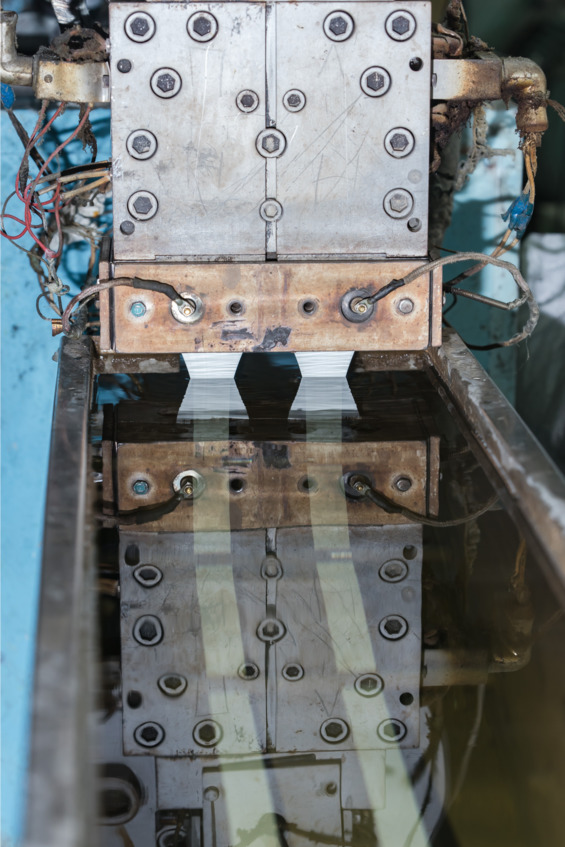
Выход расплава в охлаждающую ванну
4-й этап. Охлаждение
На выходе из экструдера, еще горячую, несформированную ленту, протягиваю по низу охлаждающего резервуара (его еще называются охлаждающей «ванной») для последующего закрепления на растягивающих валах.
5-й этап. Формирование ленты и процесс растяжения
Предварительно охлажденная лента протягивается через множество валов. Их функция – растянуть ленту и начать формировать ее вид и размер.
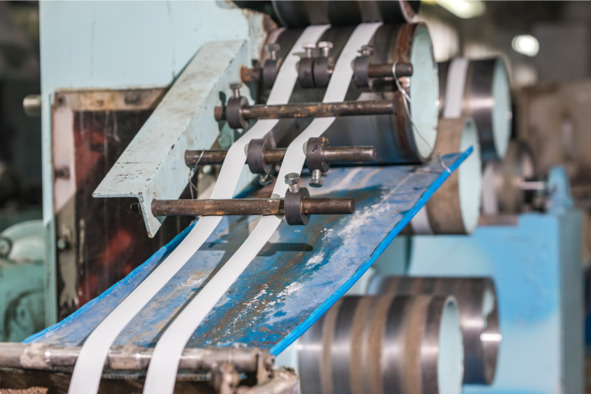
Процесс растяжения ленты и формирование ширины
6-й этап. Повторный цикл охлаждения
После первой растяжки, лента проходит повторный цикл охлаждения. Растянутый материал начинает приобретать конечную форму по заданному типоразмеру.
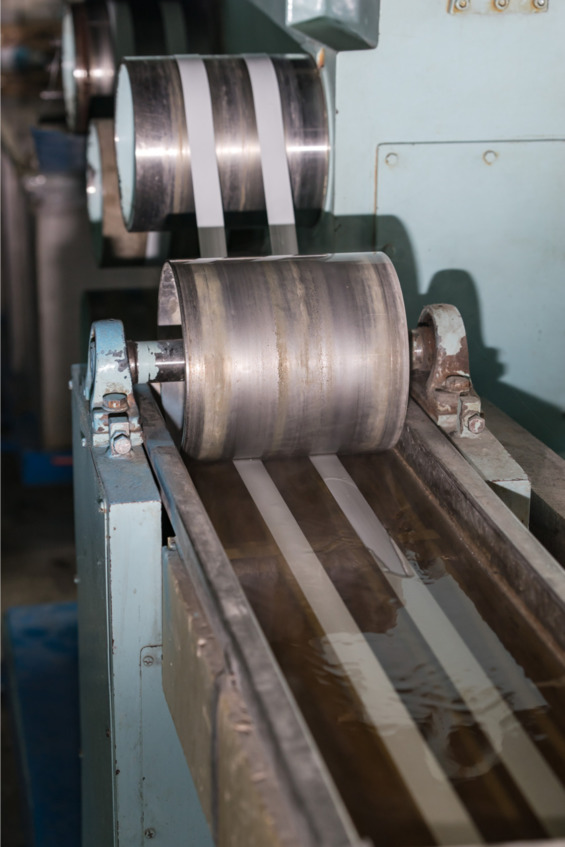
Повторный цикл охлаждения
7-й этап. Подготовка к формированию насечки
В процессе растяжения лента уменьшается в размерах от 40 до 70%, и после нескольких циклов охлаждения становится готовой к формированию насечки.
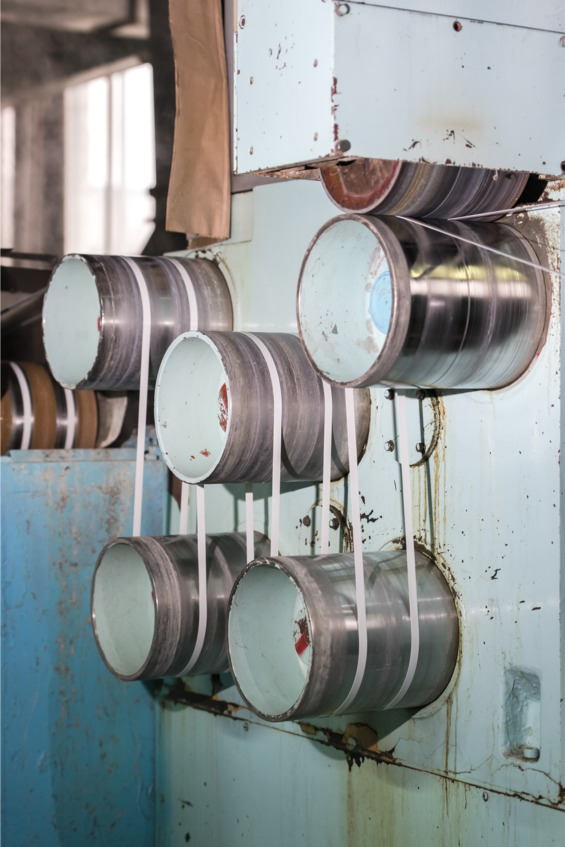
Процесс растяжения ленты
8-й этап. Протяжка ленты через формующие валы
После цикла охлаждения и растяжки ленту пропускают через формующие валы, имеющие выпуклую поверхность.
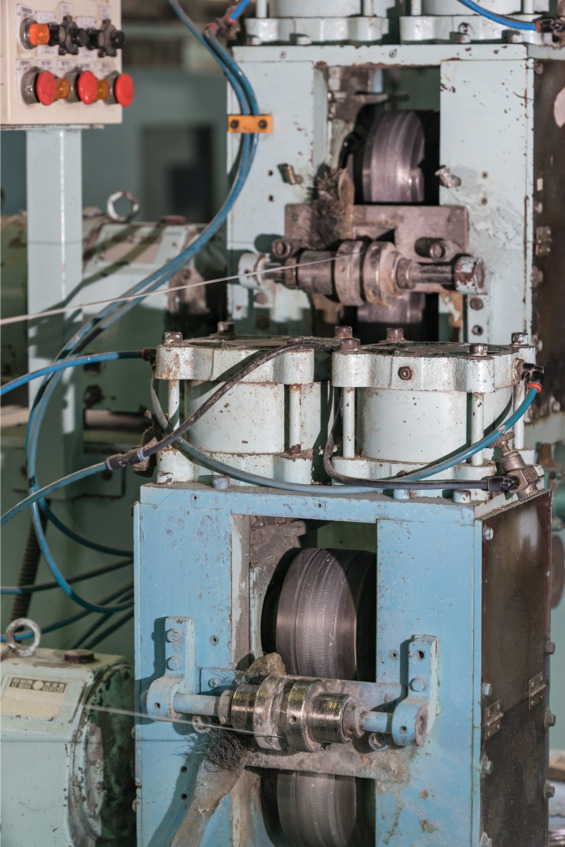
Формирование насечки на ленте
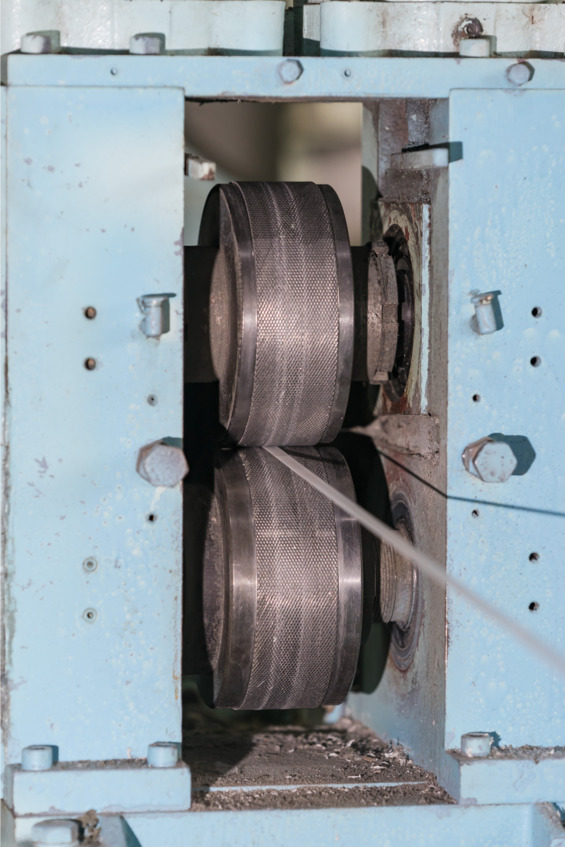
Лента проходит между двух насечных валов
9-й этап. Формирование насечки
Еще 10 лет назад вся лента делалась без насечки, но впоследствии для снижения удельного веса ленты, а следовательно себестоимости, была придумана насечка.
Лента с насечкой и гладкая лента одинаково держатся в скобе и не проскальзывают при натяжении, что было подтверждено тестами на разрывной машине.
10-й этап. Стабилизация
На одном из последних этапов производства, проводится стабилизация молекулярной структуры изготавливаемой ленты, а также снятие внутренних напряжений
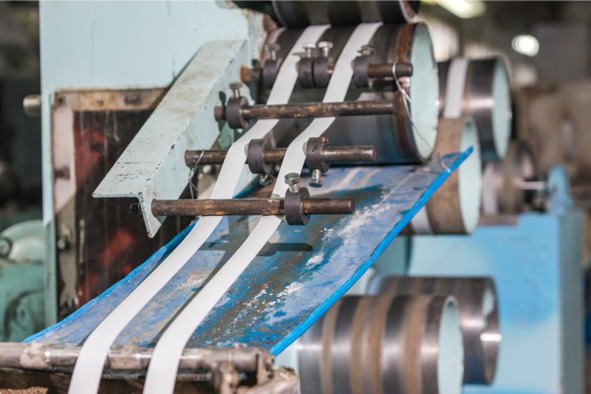
11-й этап. Цикл сушки ленты
После прохождения всего процесса формирования, охлаждения и нанесения насечки, лента должна пройти цикл сушки. Обычно лента просто висит в натянутом состоянии на расстоянии 5—10 метров от последней машины растяжения до конвейера, осуществляющего намотку на картонную шпулю.
12-й этап. Намотка ленты на картонную шпулю
Намотка производится в несколько рядов на одном уровне по поверхности картонной втулки. В намотчике установлено контрольное окно, которое не допускает намотку ленты ненадлежащего качества. Электронные намотчики проходят ежегодную поверку и гарантируют точность намотки до 1 метра.
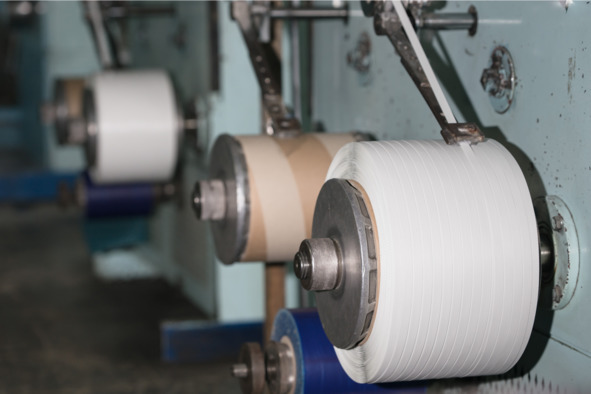
Финал производственного процесса – намотка ленты на картонную шпулю
2.3. Сырьевые компоненты в производственном процессе
В процессе производства в полимерные ленты добавляются определенные сырьевые добавки, для придания ленте определенных физических свойств, соразмерно стоящим перед ней задачам. Это могут быть и цветные красители, и модификаторы, влияющие на эластичность.
Например, одна и та же лента ПП может не работать на автомате Mosca, но прекрасно себя чувствовать в Transpak.8
Основные добавки и компоненты отражены в таблице:
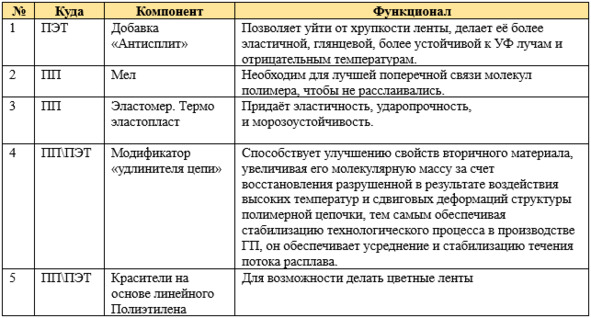
Таблица 8. Компоненты и добавки
2.4. ТУ и контроль качества
Любое производство подразумевает технологию и стандарты, по которым будет изготавливаться продукция. В свою очередь, чтобы продукция была стабильно высокого качества, придумываются различные методики контроля, как на этапах производственного процесса, так и уже готовой продукции.
ГОСТ 21214—759 был разработан еще в 1975 году, когда неметаллических лент для упаковки продукции в продаже еще не было. СССР прекратил своё существование, на постсоветском пространстве появились полимерные ленты, но бюрократические механизмы изменяются, всё так же, с большим скрипом. Именно поэтому, как такового ГОСТа для полипропиленовой ленты в РФ нет, и приходится ориентироваться на общепринятый 21214—75, который будет действовать до 01.11.2082.
Но кроме официальных ГОСТов у каждого производителя имеется ТУ, оформленные в установленном государством порядке. По ним и осуществляется в данный момент выпуск всех стреппинг-лент в РФ.
Контроль качества готовой продукции по типам можно разделить на внешний и внутренний.
Внешний осуществляется сторонними компаниями-аудиторами, центрами сертификации и лабораториями.
Внутренний проводится силами производителя, непосредственно на месте.
А вот уже по видам, контроль качества бывает:
– первичный. Осуществляется на производстве, путём отбора проб сразу после производства партии продукции.
– постпродажный. Его осуществляет Клиент на своем производстве, после получения ленты от производителя. Также, его часто проводят специалисты производства непосредственно на территории Клиента, с целью сравнения произведенной ленты с аналогичными образцами конкурентов.
Важно понимать, что каждая произведенная партия ленты уникальна. Качество сырья, работа оборудования, температурные воздействия, человеческий фактор – всё это оказывает непосредственное влияние на изготовление очередной партии. Однако, не смотря на силу и непредсказуемость этих факторов, лента должна соответствовать определенным нормам, чтобы выполнять свои функции.
В процессе производства на определенных этапах делается контроль качества, заключающийся прежде всего в замере показателей соответствия ширины и толщины ленты заданным параметрам. Так, лента 9-мм не может на выходе превращаться в 12-мм. Для этого, с помощью штангенциркуля, операторы линии периодически проверяют ленту.
Отбор проб и последовательность проверки качества продукции:
1. Полипропиленовая лента принимается ОТК партиями. Партией считается количество роликов одного размера, цвета, сложенными на одном паллете с присвоенным номером партии.
2. Проверке внешнего вида партии подвергают 100% роликов.
3. Количество роликов, подлежащих проверке, в зависимости от объема партии, представлены в таблице №1.
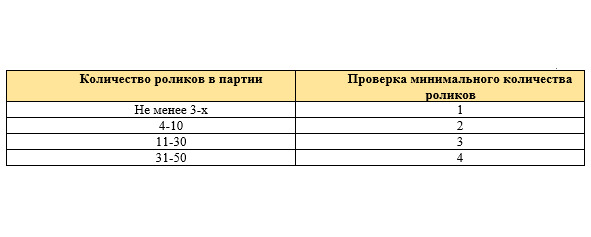
Таблица 9. Проверка роликов
4. Выборку роликов с паллеты осуществляют в произвольном порядке, но таким образом, чтобы были учтены особенности проверки качества.
Контролер ОТК все значения параметров заносит в специальный журнал. О наличии замечаний по в срочном порядке докладывается мастеру или технологу.
При получении отрицательных результатов испытаний хотя бы у одного проверенного ролика из числа необходимого минимального количества или хотя бы по одному показателю – проводят повторные испытания по этому же показателю на удвоенном количестве роликов, отобранных из той же партии.
Если после повторных испытаний результат положительный – партия считается принятой ОТК.
Если после повторных испытаний хотя бы по одному показателю получен отрицательный результат, контролер ОТК сообщает мастеру/технологу и они должны решить вопрос о судьбе партии.
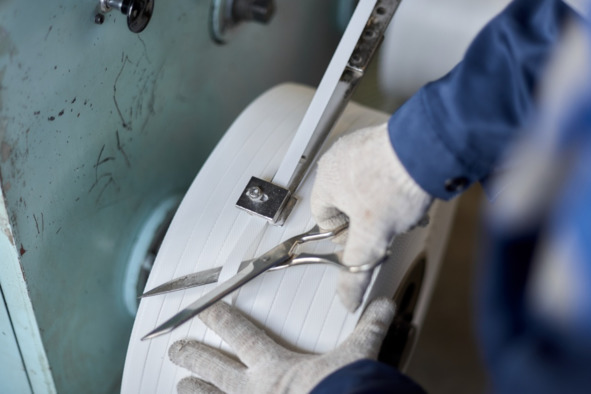
После остановки намотки, конец ленты обрезается. Бобина снимается с намотчика и отправляется на испытания и последующую упаковку
Каждый ролик, взятый на контроль из партии проверяется на соответствие следующим параметрам:
1. Вес бобины;
2. Метраж;
3. Ширина;
4. Толщина
5. Усилие на разрыв;
6. Саблевидность;
7. Деформация;
8. Равномерность тиснения;
9. Отсутствие заусенцев, расслоений-мохристости, царапин, следов от загрязнённых валов тиснения и пр. предметов;
10. Отсутствие продольной полосы следов от «бороды» -загрязненная матрица;
11. Отсутствие разрывов, зазубрин;
12. Отсутствие разводов (для цветной).
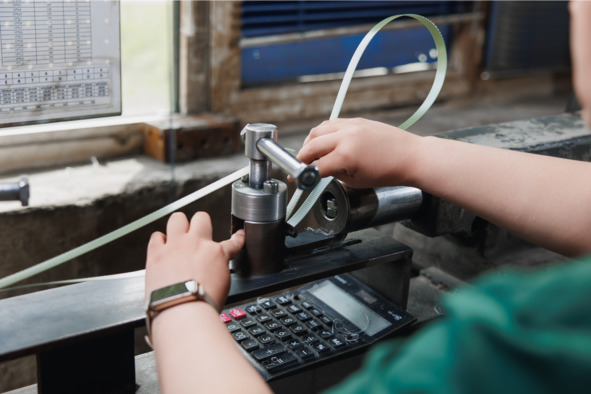
Процесс заправки ленты в разрывную машину
Каждой партии изготавливаемой ленты присваивается свой уникальный номер, благодаря которому любую партию можно отследить и проверить на соответствие нормам ТУ. Для множества государственных компаний, закупающих ленты через тендерные площадка, паспорт качества является обязательным сопроводительным документом к товару, без которого приёмка осуществляться не будет.
После всех контрольных мероприятий, на ленту делается паспорт качества:
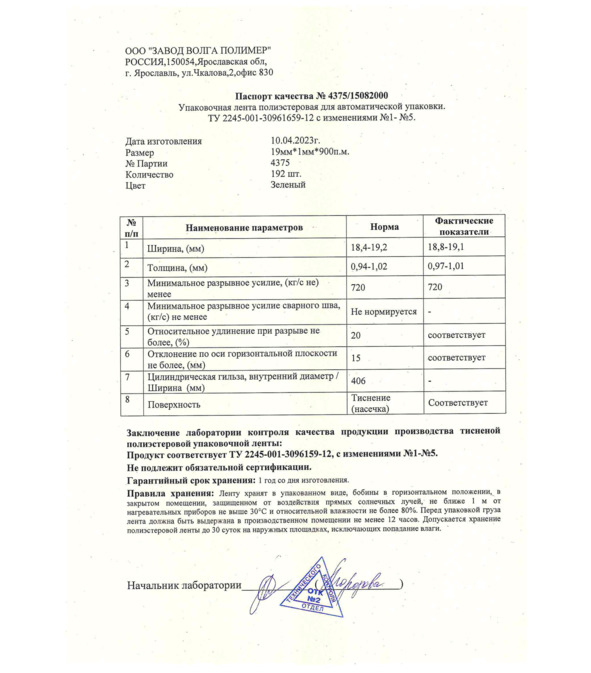
Пример паспорта качества на партию ленты ПЭТ 19х1, проверенную ОТК
Кроме базовых замеров, качество ленты определяется следующими показателями:
1. Серповидность – влияет на скорость и качество работы оборудования;
Серповидность (саблевидность) ленты – геометрический параметр и качественный показатель, который характеризует прямолинейность ленты при разматывании из бобины на автоматических стреппинг машинах. Когда автомат выстреливает ленту – она должна двигаться в точно заданном направлении, чтобы пролететь по рамке автомата и попасть в упаковочную головку. Если серповидность повышена, то лента застрянет в рамке, будут происходить сбои в работе оборудования, возникнут дополнительные отходы ленты, процесс обвязки замедлится.
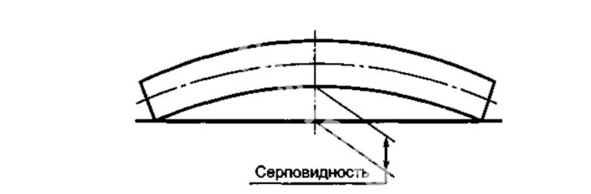
2. Разрывная нагрузка – влияет на надежность крепления груза.
Разрывная нагрузка измеряется в кгс (килограмм-сила)10, и означает предельное усилие, которое выдерживает лента на предмет разрыва. Например, разрывная нагрузка ленты равная 300 кгс означает, что при нагрузке на ленту массы в подвешенном состоянии вес в 300 кг является предельным, и после превышения которой может последовать разрыв ленты.
3. Относительное удлинение (или упругое восстановление) – способность кратковременно воспринимать нагрузки и возвращаться в исходное положение.
Одно из преимуществ полипропиленовых лент – эластичность, или возвратная память, что очень важно при складировании, хранении и перевозке грузов, т. к. наличие эластичной памяти повышает стойкость ленты к ударным нагрузкам. В процессе перевозки устойчивость груза может быть нарушена, а стальные ленты зачастую растягиваются от веса груза, так же нередки прогибы и провисания ленты. За счет эластичности, полипропиленовые ленты при растяжении возвращаются в исходное положение без потери упругости.
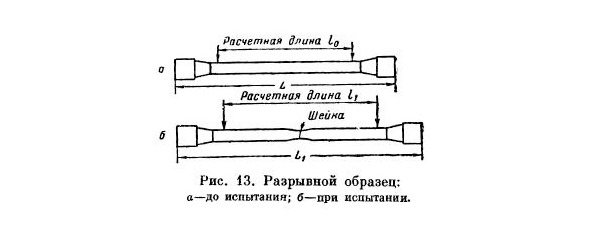
Определяют разрывную нагрузку и относительное удлинение с помощью разрывной машины вертикального типа или горизонтального типа, аттестованной в установленном порядке.
Ленту заправляют в зажимы разрывной машины (во избежание проскальзывания и перекусывания ленты в плоских зажимах допускается применение прокладок из наждачной бумаги). Показания снимаются в момент остановки показаний прибора.11
Удлинение при разрыве (L) определяют одновременно с определением разрывной нагрузки, и вычисляют по формуле в процентах:
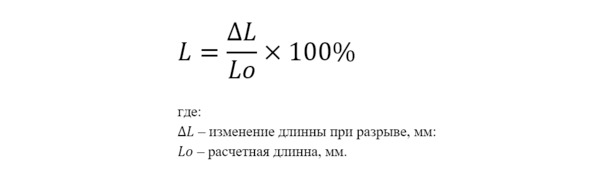
За окончательный результат определения разрывной нагрузки и удлинения ленты принимают среднее арифметическое результатов 3-х первичных испытаний.
При производстве ленты, на эти три показателя напрямую влияет не только использование высококлассного оборудования, но и добавление в сырье вторично-переработанных материалов. Вторсырье делает ленту более хрупкой, менее эластичной, а ее серповидность увеличивается.
2.5. Полимерные ленты с логотипом
Производство полимерных лент с логотипом технологически ничем не отличается от производства обычных лент. Сперва на экструзионной линии изготавливается сама лента, после чего устанавливается на специальный станок по нанесению логотипа.
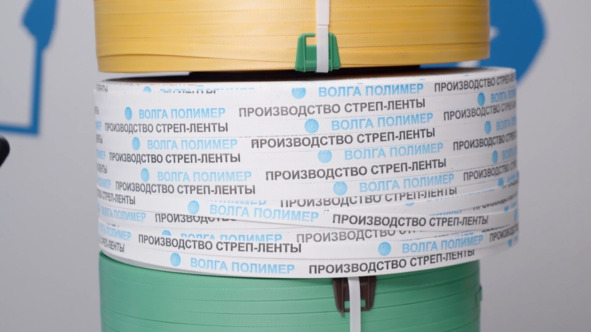
Для того, чтобы нанести логотип, требуется изготовить клише из полимерной резины, с логотипом клиента, и определиться с выбором краски. Клише имеет продолговатую продольную форму и закрепляется на круглые наносящие валы, которые окунаются в краску, после чего отпечатывают логотип на ленте.
В качестве логотипа не рекомендуется брать картинки с большим количеством мелких деталей, т.к. из-за особенностей производства они будут трудночитаемы или совсем невидимы. Чаще всего на ленту наносятся: логотип компании, название, доменное имя сайта, контактный телефон.