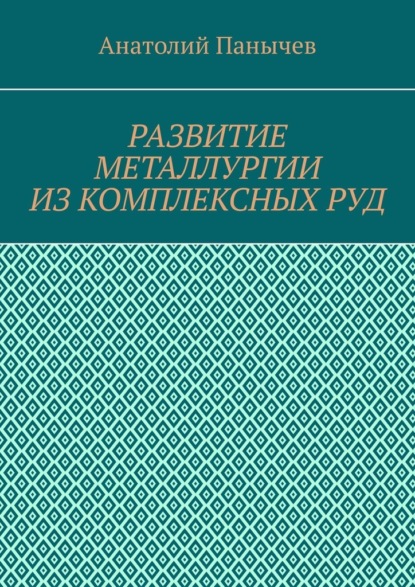
Полная версия:
Развитие металлургии из комплексных руд. История металлургии
Крепость руд. Наибольшей крепостью обладают конгломерато-оолитовые, оолитовые и плотные латеритовые руды. Руды конгломерато-оолитовые и оолитовые (2 и 3 горизонтов) большей частью имеют плотное массивное сложение. Они обычно обладают наибольшей крепостью, что объясняется наличием в руде большого количества прожилков плотного афанитового гидрогетита.
Латеритовые руды в основном сложены глинистым и алевритовым материалом, менее массивны и, большей частью, имеют значительно меньшую крепость. Глинистые частицы латеритовых руд имеют разную степень уплотнения и, следовательно, в зависимости от этого – различную крепость. Кроме процессов уплотнения (в узком понимании этого термина) на крепость латеритовых руд большое влияние оказываю процессы цементации, в результате чего первоначально рыхлая масса может приобрести большую крепость.
Цементом латеритовых руд может служить плотный афанитовый гидрогетит и кремнекислота.
Крепость рыхлых латеритовых руд иногда связана с явлением скелетообразования, то есть образованием густой сети тонких взаимно пересекающихся, кварцевых прожилков, хорошо скрепляющих всю рудную массу.
Рудный делювий (к этому типу руд мы относим так называемые глиноземистые руды, которые имеют некоторое распространение в верхах рудной толщи) большей частью представлен глинистыми разновидностями руд с подчиненным количеством массива. Отдельные куски руд иногда обладают высокой прочностью.
Пылеватость руд. Латеритовые руды содержат значительное количество пылеватых частиц. Конгломерато-оолитовые и оолитовые руды пылеватых частиц содержат значительно меньше. Порошковатые, охристые (латеритовые) руды состоят целиком только из пылеватых частиц. Механический анализ порошковатых руд показывает, что в составе их преобладают мелкие, почти дисперсные частицы.
Механический состав порошковатых руд:
Диаметр частиц в мм Содержание в %
0,5 – 0,25 1,5 – 2,0
3,25 – 0,05 1,9 – 2,0
0,05 – 0,01 30 – 32
0,01 – 0,005 20,0
0,005 – 0,001 15,0
меньше 0,001 12,0
Форма частиц – тонко-чешуйчатая, на что указывают явления каогуляции (свертывания частиц), наблюдающиеся при производстве механических анализов. Содержание пылеватых частиц в разных типах ориентировочно определяется следующими величинами:
Содержание пылеватых частиц, в %
1 Конгломерато-оолитовые 10—25
2 Оолитовые 10—20
3 Латеритовые плотные 15—25
4 Латеритовые довольно плотные 20—35
5 Латеритовые порошковые охристые 90—100
Кусковатость руд. Характерной особенностью руд Орско-Халиловской группы месторождений является большой выход мелких классов, так выход мелочи менее 10мм при добыче руд Аккермановского месторождения достигает до 75%, а после предварительной подготовки руд Новокиевского и Новопетропавловского месторождений к доменной плавке на дробильно-сортировочной фабрике отсев мелочи менее 10мм достигал до 40—50%. При разработке, наряду с крупными кусками руд, получается значительное количество мелочи. По кусковатости разные типы руд резко отличаются друг от друга. Например, конгломерато-оолитовые и оолитовые руды при экскаваторной добыче обычно дают большие глыбы размером до 0,5 м, которые требуют дробления перед пуском их в доменную плавку.
Латеритовые руды, обладающие трещиноватостью, а также грубой и тонкой слоистостью, при разработке дают более мелкий и кусковатый материал с большим количеством мелочи.
Трещиноватость рудной толщи, наиболее развитая в латеритовых рудах, но свойственная также и переотложенным рудам, определяет способность руд к окускованию при добыче. Поэтому среди всех типов руд по этому признаку могут быть выделены руды крупно-, средне- и мелкокусковатые. Развитие трещиноватости, по-видимому, тесно связано с новейшими тектоническими нарушениями и там, где они проявляются наиболее интенсивно, трещиноватость имеет максимальное распространение. Исходя из вышеизложенного можно предполагать, что западная (сброшенная) часть Новопетропавловского месторождения имеет наиболее развитую трещиноватость и представлена наиболее кусковатыми рудами.
Рудный делювий (1 горизонт), имеющий весьма широкое распространение на всех месторождениях и слагающий верха рудной толщи, представляет собой мелко- и среднекусковатый материал с большой примесью пылеватой массы пустых пород, которая заполняет пространство между отдельными кусками руды. При добыче этих руд получается большое количество мелочи, состоящей из нерудных компонентов, что позволяет путем грохочения отделить более богатую руду (кусковатую) от бедных примесей.
Химические анализы руды показали широкий размах колебленности элементов
Среднее содержание в руде основных элементов приведено в табл. 3:
аблица 3
Содержание элементов в рудах Орско-Халиловской группы месторождений
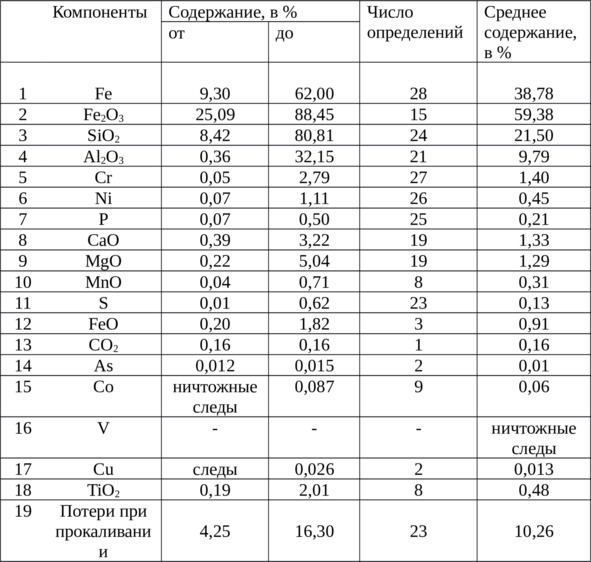
Технология обогащения Орско-Халиловских руд имеет много специфических особенностей и требует углубленного научно-исследовательского анализа. Исследователями доказано, что наиболее приемлемыми методами обогащения Орско-Халиловских руд являются пирометаллургические (обжигмагнитный, кричномагнитный). При обжигмагнитном методе обогащения увеличивается диспергация всего рудного материала, ослабляются контакты (связь) между минеральными частицами и повышается полнота раскрытия рудных зерен.
Автором изучена зависимость показателей обжигмагнитного обогащения от содержания железа в исходном руде. Результаты проведенных 11 опытов с содержанием железа в исходной руде в интервале от 24,4 до 43,3% приведены в табл.4. Графическая обработка показателей показана на рис.1
Таблица 4Результаты опытов по обжигмагнитному обогащениюприроднолегированной руды с различным содержанием железав исходном продукте.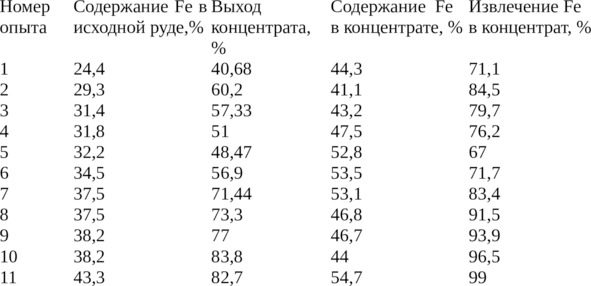
Из графиков рис.1 видно, что повышение содержания железа в исходном продукте от 24,4 до 29,3% влечёт резкое повышение выхода концентрата от 40,68 до 60,2% и извлечения железа в концентрат от 71,1 до 84,5%, но при этом снижается содержание железа в концентрате от 44,3 до 41,1%. Повышение железа в исходном продукте с 29,3 до 32,2 приводит к снижению выхода концентрата с 60,2 до 48,47% и извлечения железа в концентрат от 84,5 до 67%,, при этом, содержание железа в концентрате поднимается от 41,1 до 52,8%. Дальнейшее повышение содержания железа в исходном сырье ведёт к повышению извлечения и выхода железа в концентрат, однако, содержание железа в концентрате медленно падает с 52,8 до 44%. В богатых же рудах (38,2 – 43,3%) содержание железа в концентрате возрастает с 44,0 до 54,7% при значительно высоком извлечении (96,5 – 99%) и выходе концентрата (83,8 – 82,7%).
Следует отметить, что поведению легирующих примесей в условиях процесса ранее не было уделено достаточного внимания. Главным компонентом, на который и был нацелен весь процесс обогащения, являлось железо. Однако, следует учитывать, что физические свойства минералов основных и легирующих элементов, которые в одинаковой степени важны для оценки качества руд – различные, а поэтому в условиях одних и тех же методов обогащения различные компоненты руд будут вести себя по разному и, естественно, что получение положительных результатов обогащения по одному железу не даёт достаточных оснований для положительной оценки испытываемого метода или схемы обогащения, так как неудовлетворительные результаты по легирующим элементам могут свести к нулю эффективность обогащения. Зная ассоциационные свойства минералов железа и легирующих элементов возможно прогнозирование и планирование экспериментов и технологических схем обогащения.
Современный уровень исследований позволяет считать оптимальными следующие методы обработки руды.
Для дробления Орско-Халиловских руд обоснована необходимость использования молотковой дробилки при режиме работы с регулируемым числом оборотов ротора с нижним пределом скорости вращения 300 об/мин [1]. Установлена возможность грохочения сырых (12—25%) бурожелезняковых руд на вибрационных грохотах с электроподогревом сеток с эффективностью до 80% [2].
Получены результаты исследования измельчаемости обожженной руды, которая до крупности 45% класса – 0,071мм измельчается легче руды ЮГОКа (коэффициент измельчаемости находится в пределах 1,90—1,0), при более тонком измельчении обожженную руду можно отнести к категории прочных руд (коэффициент измельчаемости снижается по отношению к руде ЮГОКа до 0,67). Измельчаемость обожженной природнолегированной руды в диапазоне крупности от 20 до 60% класса – 0,071мм примерно на 40% ниже измельчаемости сырой лисаковской руды. При более тонком измельчении коэффициент измельчаемости приближается к 1,0 [3].
Исследования обогатимости Орско-Халиловских руд показали, что сухая магнитная сепарация обожженной руды со степенью обжига 124%, крупностью 6—0мм обеспечивает более высокое извлечение железа (94,20%) и кобальта (91,47%) в магнитный продукт, но содержание в нем железа составляет 44,8%. Сухая магнитная сепарация позволяет вывести из процесса хвосты с показателем, %:

Исследование обогащения мокрой магнитной сепарацией позволило установить возможность при измельчении в две стадии до 20% класса – 0,071 мм и 70% класса – 0,071мм получить концентрат с перечисткой по качеству удовлетворяющему промышленность (3-ей группы); %:
Fеобщ = 58,74; Ni = 0,62; Сr2О3 = 0,91; Со = 0,094;
S= 0,003; ТiО2 = 0,31; МgО = 0,69; СаО = 5,31;
АI2О3 = 5,66; SiО2 = 12,48.
Выход концентрата составляет 43,86% при извлечении железа, никеля, кобальта и хрома соответственно 76,18; 58,77; 60,45; 30,70%.
Поведение легирующих компонентов в процессе обогащения отражено на рис. 2, 3. Из графиков рис.2, 3 видна слабо выраженная ассоциационная зависимость элементов. Так, графики рис.2 показывают, что в интервале содержания железа от 13,72 до 28,68% хром имеет большую колеблемость, не показывая какую-либо закономерность При дальнейшем повышении железа до 58,74% содержание хрома имеет тенденцию на снижение (от 1,85 до 0,62%). При интервале содержания железа от 13,72 до 16,42% содержание никеля увеличивается от 0,32 до 0,48%, затем при интервале содержания железа от 16,42 до 25,01% содержание никеля падает от 0,48 до 0,41%, дальнейшее повышение железа в продуктах (вплоть до 58,74%) ведёт к повышению в них никеля от 0,41 до 0,62%.
Ассоциационная зависимость наблюдается также у элементов никеля и кобальта (рис.3). Так, при содержании никеля 0,32%, кобальт равен 0,044%; повышение содержания никеля до 0,48% ведёт к увеличению кобальта до 0,08%, снижение же содержания никеля от 0,48 до 0,41% приводит к соответствующему снижению кобальта от 0,08 до 0,06%. Дальнейшее повышение содержания никеля в прдуктах обогащения от 0,41 до 0,62% приводит к несоразмерному повышению кобальта от 0,06 до 0,094%.
Для выявления оптимальной степени магнетизирующего обжига автором исследовались руды на обогатимость по двухстадиальным схемам при степенях восстановления равным 36,3; 63,0; 104,0; 135,0; 157,0; 162,0%. Результаты обогащения руды, восстановленной при выше указанных степенях восстановления, показаны на приведенных схемах (рис.4).
Проведенные исследования позволили разработать рациональную технологию обогащения природнолегированной руды (рис. 5). Дробление руды предусматривается в две стадии молотковыми дробилками (с регулируемой скоростью вращения ротора, ограниченной по нижнему пределу 300 об/мин). Конечная крупность дробления руды – 12—0мм.
Перед магнетизирующим обжигом предусмотрена сортировка руды на классы 12—6, 6—0мм и раздельный их обжиг.
Обожженная руда подвергается сухой магнитной сепарации, что позволяет вывести из процесса 14,29% бедных железом (13,72%), никелем (0,32%) и кобальтом (0,044%), но богатых хромом (1,99%), хвостов.
Промпродукт сухой магнитной сепарации (Fе = 44,8%; ε = 94,20%) направляется на измельчение до 20% класса – 0,071мм, а затем на сухую магнитную сепарацию, где удаляется из процесса 20,9% хвостов с содержанием железа 16,42%, никеля 0,48%, кобальта 0,08%, хрома 1,27% при извлечении соответственно 7,56; 12,39; 25,12; 30,19%.
Промпродукт сухой магнитной сепарации (Fе = 50,61%, ε = 86,64%) подвергается доизмельчению с предварительной и поверочной классификацией до 70% класса – 0,071мм в шаровой мельнице. Удельная производительность шаровой мельницы при измельчении промпродукта мокрой магнитной сепарации по класу – 0,071мм составляет q0,071 = 1,340 х 0,40 = 0,536 т/м3ч. После доизмельчения промпродукт подвергается перечистке мокрой магнитной сепарацией с получением концентрата, содержащего Fе = 58,7, Ni = 0,62, Со = 0,094 и Сr = 0,62%, при извлечении соответственно 76,18; 58,77; 60,45; 30,70%.
Общие хвосты содержат Fе = 19,42; Ni = 0,45; Со = 0,062 и Сr = 1,57%, при извлечении соответственно 23,82; 41,23; 39,55; 69,30%.
Окускование.
Нами на Орско-Халиловском металлургическом комбинате были проведены исследования с целью определения оптимальных условий получения офлюсованного известняком агломерата из Новокиевской рудной мелочи с добавлением крицы, прекрасным сырьем для которой является руда Аккермановского месторождения [6].
В процессе исследований изучалось влияние на процесс агломерации четырех факторов: содержание в шихте углерода, известняка, крицы и Новокиевской руды, а также высоты слоя шихты на аглоленте.
Влажность шихты изменялась в пределах от 7,5 до 9,5%.. Выявлено, что удельная производительность, вертикальная скорость и газопроницаемость возрастают с увеличением влажности шихты.
Изучалась зависимость технологических параметров от изменения основности агломерата. Основность агломерата при отыскании оптимального уровня повышалась от 0,3 до 2,5. С увеличением основности агломерата несколько падает выход годного агломерата из спека, а за счет увеличения вертикальной скорости спекания удельная производительность возрастает.
Исследовали также зависимость технологических параметров от содержания Новокиевской руды в шихте и крицы.
Результаты исследований показали, что наиболее оптимальные условия спекания следует считать при содержании в шихте крицы 28—35%, Новокиевской руды 13%. Дальнейшее увеличение содержания крицы в шихте приводит к снижению удельной производительности агломерационной установки. Новокиевская руда (в количестве до 13%) увеличивает вертикальную скорость спекания, а, следовательно, и удельную производительность аглоустановки. Прочность агломерата с повышением основности до 2,2—2,5 улучшается, а известняк интенсифицирует процесс спекания.
Другой рациональный путь подготовки Орско-Халиловских руд к доменной плавке следует считать агломерацию их в смеси с привозными концентратами.
Так, опытные спекания, проведенные на ОХМК, смеси Новокиевской руды с Соколово-Сорбайского концентрата дали качественный агломерат и таким способом показали целесообразность использования руд Орско-Халиловского района.
Спекание проводили при соотношении Новокиевской руды 53,5% и Соколово-Сорбайского концентрата 46,5%. При опытном спекании получена удельная производительность: по выходу годного агломерата – 1,14т (м2) час – 1,24т (м2) час; по железу в агломерате – 0,53т (м2) час – 0,58т (м2) час.
Результаты исследований [7] и математическая обработка годовых технологических параметров [8] позволили выявить возможности интенсификации процесс агломерации и повышение качества продукта.
Существенными из них для данного типа руд являются оптимизация газодинамических параметров процесса спекания с увеличением разрежения под колосниковой решеткой до 16 – 19 кПа при сокращении подсосов постороннего воздуха; предварительный подогрев шихты; ввод в шихту известняка и извести (пушонки); применение метода двухслойного спекания; улучшение качества смешения шихты; повышение газопроницаемости шихты добавками крупнозернистых руд.
Увеличение производительности агломашин и улучшение качества агломерата обеспечивается за счет оптимизации газодинамических характеристик агломашин. Совершенствование элементов газового тракта, сокращение подсосов постороннего воздуха – важный резерв повышения технико – экономических показателей процесса спекания. Так, по обобщенным данным, снижение относительного количества подсосов постороннего воздуха только на 1% обеспечивает снижение расхода электроэнергии на 0,8 – 1,8% и увеличение производительности на 0,2 – 0,8% (40).
Перспективным направлением интенсификации процесса спекания является повышение разрежения под колосниковой решеткой до 16 – 19 кПа за счет разработки и создания высоконапорных эксгаустеров в сочетании с разработкой эффективных конструкций продольных и торцевых уплотнений агломашин.
Существенный эффект в увеличении производительности установки и улучшении качества агломерата может обеспечить технология спекания шихты при избыточном давлении газов в слое (до 200 – 300 кПа) в высоких и сверхвысоких (0,8 – 1,3 м) слоях. Однако эта технология требует разработки конструкции технологичного и надежного агрегата.
Сущность способа с подогревом шихты заключается в том, что в ходе процесса агломерации в подогретой шихте не происходит конденсации влаги, благодаря чему поддерживается более высокая газопроницаемость слоя шихты. Сравнение кривых газопроницаемости и температур отсасываемых газов в процессе спекания подогретой и холодной шихт показывает одинаковый характер этих кривых. Однако продолжительность спекания подогретой шихты значительно сокращается.
Проведенные исследования, а также работа агломерационных машин на подогретой шихте до 60—70 оС показали увеличение вертикальной скорости спекания, а следовательно, и увеличение производительности агломерационных машин. Установлено, что чем мельче шихта, тем более высокий подогрев требуется для достижения более высокой производительности. Оптимальное значение температуры подогрева шихты находится в узких пределах. Подогрев шихты выше оптимального приводит к понижению производительности вследствие снижения газопроницаемости из – за подсушки шихты. Фактор предварительного подогрева шихты имеет большее значение при спекании тонко измельченных концентратов, чем при спекании необогащенных руд. Это объясняется тем, что разрушение комочков шихты при конденсации влаги сильнее сказывается на газопроницаемости слоя при спекании более мелкой шихты, чем при спекании крупной. Подогрев шихты позволяет при прочих равных условиях увеличить высоту спекаемого слоя, что повышает выход годного агломерата и улучшает качество последнего.
Конец ознакомительного фрагмента.
Текст предоставлен ООО «Литрес».
Прочитайте эту книгу целиком, купив полную легальную версию на Литрес.
Безопасно оплатить книгу можно банковской картой Visa, MasterCard, Maestro, со счета мобильного телефона, с платежного терминала, в салоне МТС или Связной, через PayPal, WebMoney, Яндекс.Деньги, QIWI Кошелек, бонусными картами или другим удобным Вам способом.
Вы ознакомились с фрагментом книги.
Для бесплатного чтения открыта только часть текста.
Приобретайте полный текст книги у нашего партнера:
Полная версия книги
Всего 10 форматов