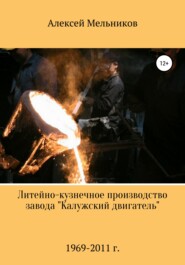
Полная версия:
Литейно-кузнечное производство завода «Калужский двигатель»
Награды
Медаль «За Трудовую Доблесть» – И.Е.Осиповский – электросварщик (1977 г.) Медаль «За Трудовое Отличие» – П.И.Темирева – резчица (1976 г.)
Медаль «За Трудовое Отличие» – В.М.Дубовкин – мастер (1977 г.)
Орден «Трудовой Славы III степени» – В.П.Пятышкина – штамповщица (1978 г.)
«Заслуженный моторостроитель» – Г.П.Киреева – формовщица (1978 г.)
«Заслуженный моторостроитель» – Н.Е.Абрамкин – плавильщик (1979 г.)
Орден «Знак Почета» – М.П.Кузнецов – токарь
Медаль «За Трудовую доблесть» – А.Н.Хохлов – слесарь
Этапы. 1975 – 1980 г.г.
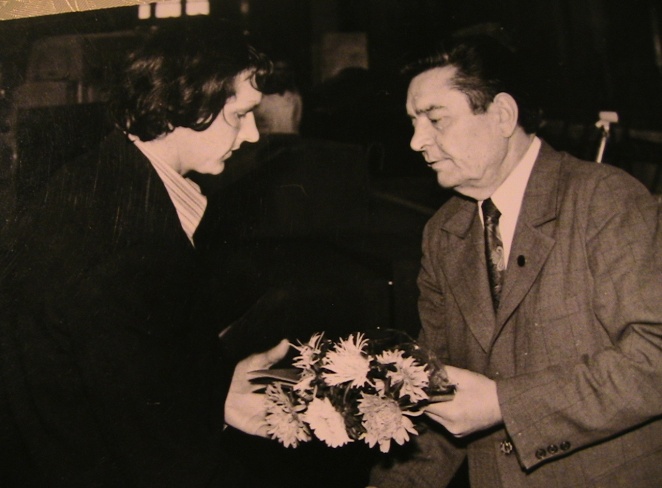
рацпредложение с экономическим эффектом 79,7 тыс. руб. Старший инженер-технолог цеха №1 Л.С.Новикова подала 6 рацпредложений, из которых было внедрено 5 с экономическим эффектом 66,8 тыс. руб. А вот один из наиболее активных рационализаторов, нынешний ветеран цеха электромонтер В.В.Яшин подал свое первое рацпредложение еще в далеком 1973 году. Всего их было у Виктора Васильевича около 15. В 80-ые годы В.В.Яшин неоднократно побеждал в соревновании лучших рационализаторов Калужского моторного завода. Ветеран и по сей день неистощим на изобретения и всевозможные усовершенствования.
Директор завода Герой Социалистического Труда П.А.Григорьев награждает активного рационализатора электромонтера литейного цеха В.В.Яшина
Следующий этап развития литейного цеха стал периодом качественной технической реорганизации. Началась реализация уникального в своем роде проекта по строительству новых литейных и кузнечных мощностей на второй площадке завода, их стремительному освоению, и, что самое главное, в безастоновочном режиме. Литейщики работали на два фронта: на старой площадке и на новой. Давала план (который, кстати, рос в те годы как на дрожжах) и осваивали новые мощности в строящихся корпусах.
Этапы. 1980 – 1990 г.г.
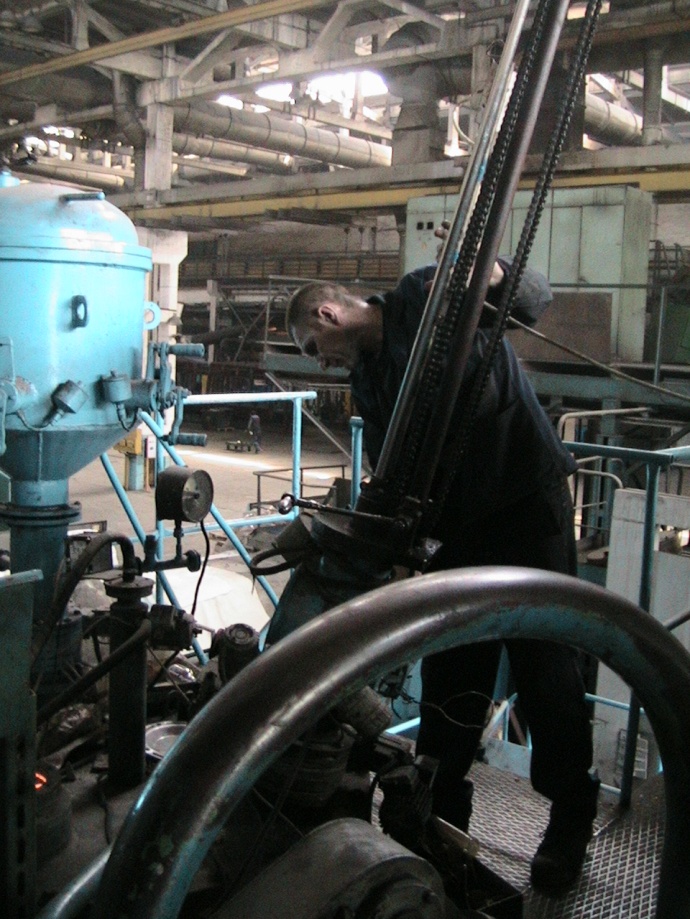
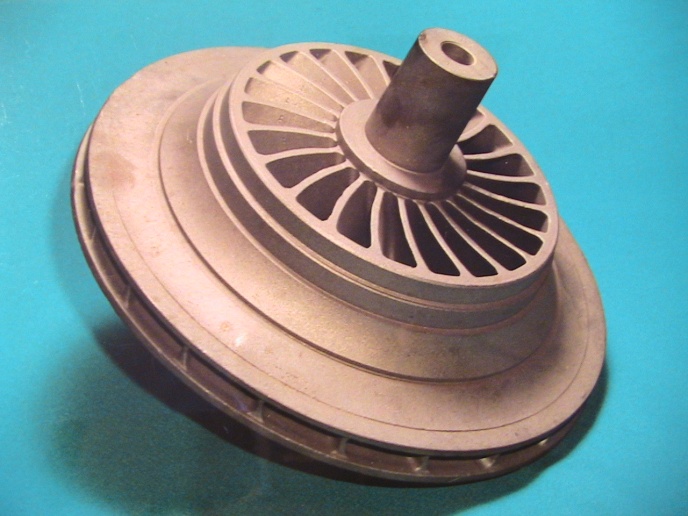
Рассказывает начальник литейно-кузнечного цеха
И.А.Балашов
: «В 1981 г. изд. 038 изготавливали до 30 единиц в месяц. В 1982 г. в январе-феврале по 40 изделий с ростом до 70 изделий в месяц на конец года. Такой темп роста объемов требовал от работников самоотдачи, энергии и чувства долга перед Родиной. Учитывая такой рост производства, Правительство и руководство завода приняли решение о создании новых мощностей литейных и кузнечных производств. Руководство завода форсировало строительство второй площадки. В 1986 г. в к.52 впервые в промышленности был осуществлен переезд литейного цеха на новую площадку без остановки производства. В 1987 году на новые площади переехало кузнечное производство и цех точного литья. Начальников цеха в этот период был
В.Е.Хайченко
, зам. начальника по производству – И.А.Балашов. Были освоены новые виды заготовок крыльчатки
I
каскада газотурбинного двигателя, работало 5 печей УППФ 3М в 3 смены и изготавливали до 120 комплектов отливок жаропрочного и атмосферного литья для изделия 029».
Плавильщик участка вакуумного литья В.В.Шадрин ведет плавку крыльчатки на печи ИСВ-016
Крыльчатка I каскада изд. 029 (ГТД -1250 танка Т-80)
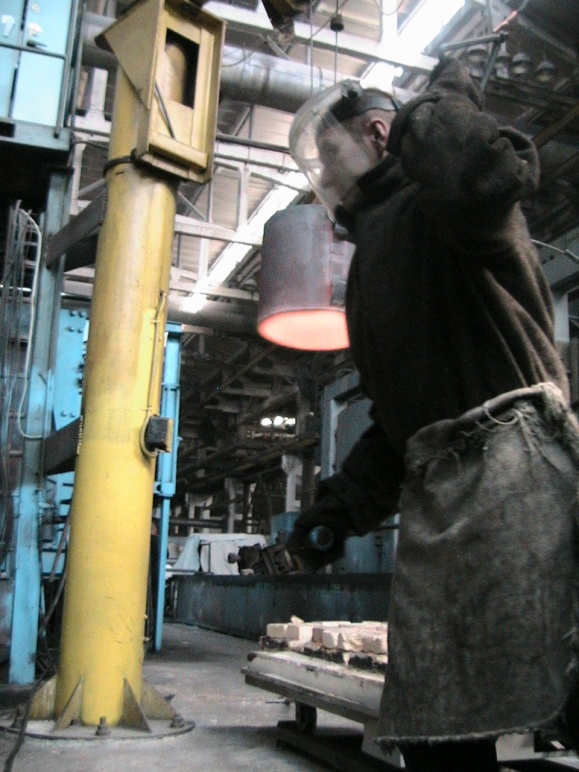
Вспоминает
В.В.Терешкин
: «В середине 80-х годов начался переезд и освоение мощностей нового литейного цеха. Сложность была в том, что надо было при этом выполнять план. Шихтовой двор был задействован в
первую очередь. Шихта готовилась на новой площадке, а плавка шла на старой. Также нужно было выделять людей для освоения нового оборудования. Например, хорошо зарекомендовавших себя вакуумных плавильных печей УППФ3М и ИСВ-016. В результате улучшились качество изделий,
и повысилась производительность. Значительно улучшились условия труда за счет подключения приточно-вытяжной вентиляции и установки грузо-подъемных механизмов. Были хорошо организованы службы электронщиков, электриков, слесарей, слесарей-вакуумщиков. Технологическое бюро было укомплектовано грамотными, работоспособными технологами, которые постоянно находились на участках, занимались повышением качества литья и освоением новых отливок и сплавов».
Этапы. 1980 – 1990 г.г.
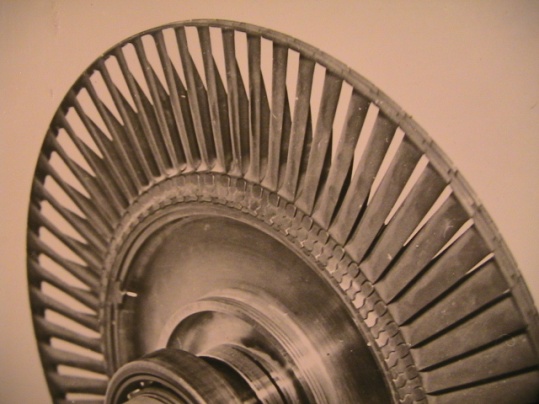
По словам старшего инженера-технолога литейно-кузнечного цеха
Л.Н.Рогачевой,
в этот период
по
цветному литью
цех освоил алюминиевое литье под низким давлением. По части жаропрочного литья было внедрено поверхностное модифицирование жаропрочных сплавов при литье лопаток с целью повышения эксплуатационных характеристик литых лопаток. Каким образом? Представим, что
жаропрочный сплав залит в форму при температуре выше 1500
о
С и вместе с ней охлаждается. Остывающий металл кристаллизуется, образуя отдельные равноосные, то есть примерно одинакового размера по всем направлениям, зерна. Сами же зерна могут получаться и крупными и мелкими. Сцепляются они ненадежно, и работающие лопатки разрушались по границам зерен и разлетались вдребезги. Ни одна лопатка не могла проработать дольше
50 часов. Тогда было предложено ввести в материал формы для литья модификатор – кристаллики алюмината кобальта. Они служат центрами, зародышами кристаллизации, ускоряющими процесс образования зерен. Зерна получаются однородными и мелкими. Новые лопатки стали работать по 500 часов. Эта технология, которую разработали в ВИАМе, работает до сих пор, и работает хорошо.
В новом 52 корпусе стали совсем другие масштабы
Одни из самых сложных по металлургии – лопатки I ступени. Тут без поверхностного модифицирования не обойтись.
Этапы. 1980 – 1990 г.г
Освоение в середине 80-х годов литейщиками и кузнецами новых производственных мощностей в корпусах 52 и 68 дало значительный прирост производственных площадей: по литью по выплавляемым моделям – 22 тыс. кв.м., по цветному литью – 16 тыс. кв.м., по кузнечному производству – 12 тыс. кв.м. На участке стального литья вводились в эксплуатацию индукционно-плавильные тигельные печи ИСТ-0,16, ИСТ-0,25, ИСТ-0,4 с емкостью тигля соответственно 160, 250 и 400 кг и временем плавки от 40 минут до 1,5 часов. Были смонтированы прокалочные печи KS-1300, KS-2000 производства Германии с температурой прокалки до 1000 градусов и мощностью до 120 квт. Установлены прокалочные печи ПВП -3000 с температурой прокалки до 1200 градусов и мощностью до 150 квт. Печи использовались для прокалки керамической оболочки под заливку лопаток газотурбинного двигателя и сопловых аппаратов. Участок жаропрочного литья был оснащен 5 вакуумными печами УППФ-3М производительностью 4-5 форм в час и емкостью тигля до 30 кг., работавшими в 3=х сменном режиме и обеспечивающими жаропрочным литьем все оборонные заказы. Отдельно под заливку крыльчаток I и II каскадов газотурбинного двигателя для танка была смонтирована и освоена вакуумная печь ИСВ-0,16 производительностью 2-3 формы в час и емкостью тигля 100 кг. Модельно керамический участок был укомплектован гидравлическим прессом ПГ-5 с усилием на штоке до 2000 кг, прессом моделей 6А50 с усилие на штоке 700 кг. Там же был установлен мощный двухкамерный паравтоклав для вытопки
В январе 1983 года в связи с производственной необходимостью и в целях дальнейшего развития мощностей литейного цеха из состава цеха №1 был выведен участок цветного литья в отдельный цех №151 (приказ по КМЗ №116 от 31.01.1983 г.). Этим же приказом начальником вновь созданного цеха №151 был назначен С.И.Малышев. Литейный же цех стал теперь под №101. Однако, проблемы ввода в строй новых литейных мощностей в корпусе 52 на второй площадке завода потребовали все-таки большей концентрации производства и управления и ранее разделенные цеха стального и цветного литья вновь были объединены в один литейный. Произошло это в 1987 году. Согласно приказа по заводу №135 от 18.02.1987 г. цеха №151 и №101 были объединены в цех №101. Начальником объединенного цеха был назначен В.Е.Хайченко.
модельной массы с установкой регенерации фирмы «Terruzzi» (Италия) и 3 вакуммно-сушильных установки УВС-3 для сушки керамических моделей в атмосфере аммиака. На участке цветного литья было установлено новое оборудование – 3 печи ИАТ-0,4 производительностью до 300 тонн алюминиевого литья в год. Численность работающих в этот период в литейном производстве достигала 720 человек.
Этапы. 1980 – 1990 г.г.
Темпы роста объемов жаропрочного литья для танкового двигателя превосходили темпы роста объемов производства самого двигателя.
Одновременно с наращиванием объемов производства происходила и модернизация самого оборонного изделия №1. Шло постоянное наращивание мощности выпускаемого калужскими моторостроителями газотурбинного танкового двигателя: сначала 1000 л.с., затем – 1100 л.с., и, наконец, 1250 л.с. (одно время прорабатывался даже вопрос о разработке двигателя мощностью 1800 л.с.). Динамика роста
мощности танка требовала аналогичной динамики и в росте жаропрочности используемых в его турбинах материалов. Разумеется, в первую очередь – самых нагруженных деталях силовой установки – лопатках, сопловых аппаратах, крыльчатках. Дело в том, что каждый дополнительный киловатт мощности газовой турбины достигается увеличением рабочей температуры в ее камере сгорания. Следовательно – усилением жаропрочностных характеристик используемых материалов. Стоит ли говорить о том, какую роль в решении этого вопроса отводилась заводским металлургам.
Этапы. 1980 – 1990 г.
«1990 год был пиком развития всего завода и литейно-кузнечного производства в частности, – говорит начальник литейно-кузнечного цеха И.А.Балашов. – Мы достигли тогда максимальных объемов по танковому двигателю (до 120 комплектов в месяц) и по малоразмерным газотурбинным двигателям 9и56 и СЭС-75 мощностью от 70 до 100 кВт, применяемых в качестве энергосистемы для запуска ракет в комплексах С-300, «Тополь», «Тунгуска». Параллельно шло освоение новых видов технологий и номенклатуры литейного и кузнечного производств. В частности на кузнечном производстве был освоен штамповочный комплекс «Weingarten» (Германия) для изготовления массивных штамповок для основных видов оборонного заказа».
Награды
«Орден Октябрьской Революции» – Г.П.Киреева – формовщица цех№1 (1981 г.)
Медаль «За Трудовое Отличие» – В.П.Волжанин – модельщик цех№1 (1981 г.)
Медаль «За Трудовое Отличие» – М.И.Дмитровский – выбивальщик цех№1 (1981 г.)
Медаль «За Трудовую Доблесть» – Л.Н.Анашкина – штамповщица цех№2 (1981 г.)
Медаль «За Трудовую Доблесть» – В.Г.Родионов – плавильщик цех №1 (1981 г.)
«Заслуженный моторостроитель» – М.М.Новикова – формовщица цех №1 (1982 г.)
«Заслуженный моторостроитель» – З.П.Авдеева – машинист цех№2 (1984 г.)
«Заслуженный моторостроитель» – В.А.Мартынов – кузнец цех №913 (1988 г.)
«Лучший рационализатор» – Л.С.Новикова – ст.инженер-технолог цех №1 (1981 г.)
– В.В.Моисеева – ст.иженер-технолог цех №1 (1985-86г.)
– В.В.Яшин – электромонтер цех №1 (1987 г.)
– В.П.Кузнецов – ст.мастер цех №1 (1988 г.)
Вот как описывала в те годы напряженный ритм работы литейщиков заводская газета «Мотор»: «Бригада выбивки литья не знает простоев. Запрессованные формы словно по конвейеру, скользят в пышущие жаром печи. Вес наиболее «солидных» из них достигает 150-200 кг. Что и говорить, работа не из легких. И, конечно же, для всего коллектива важен пример самого бригадира, который всегда на самом тяжелом и ответственном участке. Это бригадир третьего участка первого цеха М.Дмитровский… «Мои стахановцы», – ласково называет эту бригаду начальник первого цеха В.Е.Хайченко».
Этапы. 1980 – 1990 г.г.
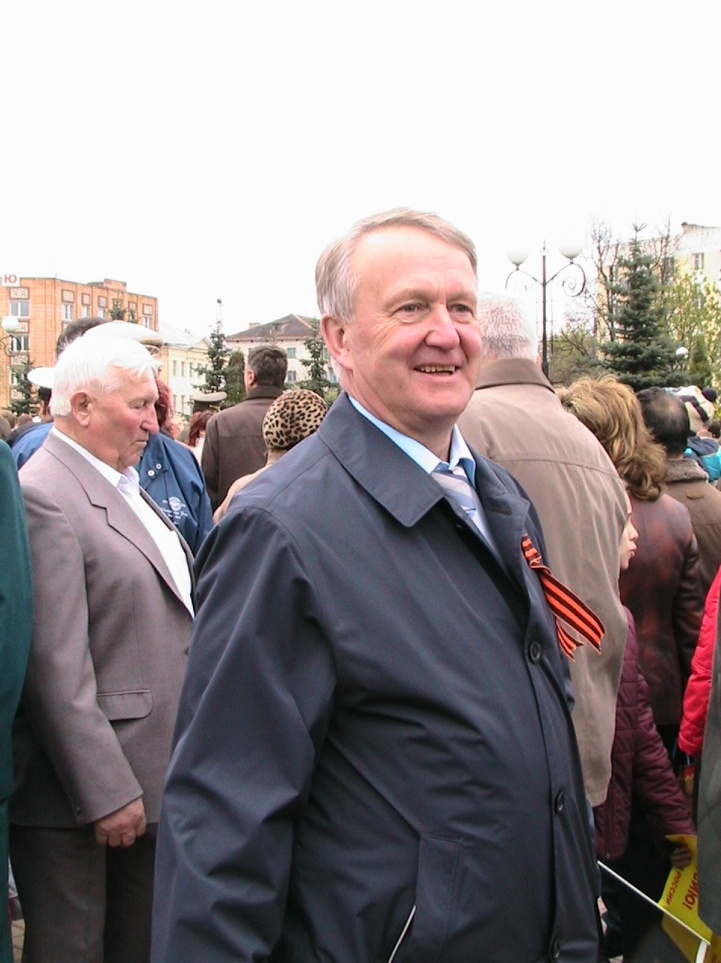
Следующий этап развития литейно-кузнечного производства был, как и для всего предприятия, самым сложным. Радикальные экономические реформы, проводимые в стране, больно ударили по предприятиям ВПК. Многие из них просто прекратили свое существование. В частности – ряд смежников КМЗ. В этих условиях уже не приходилось говорить о
каком-либо наращивании объемов, а главным образом – о выживании и поиске новых применений уникальным технологиям. Вот как охарактеризовал этот период руководитель предприятия
Ю.А.Лейковский
: «90-ые годы прошлого столетия, как и для многих предприятий-производителей ВПК, оказались самыми трудными, особенно 1996-1998 годы. Для выживания предприятия была пересмотрена его производственная деятельность, которая строилась на базе разработанных конструкторских, технических решений и целевых программ, а именно: – сохранение уникального производства газотурбинных двигателей для транспортных машин и малоразмерных ГТД в номенклатуре, освоенной предприятием под объем Гособоронзаказа; постановка на серийное производство новой системы энергоснабжения СЭС-75 на базе современного ГТД для перспективного ЗРК С-300 ПМУ с широким диапазоном
назначения и применением в народном хозяйстве; серийное производство модуля двигателя ТВ7-117 для пассажирского самолета ИЛ-114; выпуск дизельных двигателей Д12М мощностью 16, 25 л.с. для минитракторов; производство мотоблоков МБ-1Д и МБ-90 и навесных орудий к ним. На базе изделия 029 разработаны, изготовлены и отгружены силовые блоки для комплекса разрыва пластов с целью увеличения объемов добываемой нефти из скважин… Надежды на получение средств на конверсионные программы исчезли в 1995 году, когда государство перестало финансировать конверсионные предприятия. Поэтому дальнейшее освоение производства новой продукции на предприятии осуществлялось только из своих средств».
Нынешний генеральный директор Ю.А.Лейковский сумел удержать производство в трудные 90-ые годы
Этапы. 1990 – 2000 г.г.
Для литейно-кузнечного направления это было время больших структурных реформаций, реорганизаций и потрясений. В 1991 году руководство завода принимает решение о создании на базе нескольких подразделений Литейно-штамповочного завода (ЛШЗ). Через 2 года – появляется заготовительное производство с упразднением ЛШЗ. Вскоре упраздняется и заготовительное производство и реанимируется ранее ликвидированный Литейно-штамповочный завод.
Этапы. 1990 – 2000 г.г.
Частично ОГМет, ЦЛО, цех №218
Кузнечно-прессовый цех № 102
Литейный цех № 101. Начальник И.А.Балашов
Литейно-штамповочный завод (ЛШЗ). Приказ №27 от 05.02.1991 г. Директором назначен В.П.Василенко.
Заготовительное производство. Приказ №98 от 12.05.1993 г. Начальник С.И.Малышев.
Кузнечно-штамповочный цех №913. Начальник В.М.Безбородов
Цех резки и рубки металла №145. Начальник А.Г.Журавлев
Литейный цех №912. Начальник И.А.Балашов
Цех точного литья
Новый Литейно-штамповочный завод. Приказ №136 от 25.05.1998 г. Директор С.И.Малышев
Цех цветного и чугунного литья
Кузнечно-штамповочный цех
В этот период, практически лишенные гособоронзаказа, калужские моторостроители и их литейщики в том числе взялись активно осваивать гражданскую продукцию. В частности – много работали над производством дизельного двигателя средней мощности Д12М1. Нашим литейщикам пришлось осваивать производство алюминиевых отливок для этого изделия. В частности – головок цилиндров двигателя, одновременно продолжая наращивать производство литья для мотоблоков. Надо было постараться сохранить уникальное производство газотурбинных двигателей, которое, впрочем, государство по линии оборонного заказа практически не финансировало. Разрушительные реформы, реорганизации, безденежье, приватизация, сокращение персонала, жесточайшая экономия ресурсов (дело доходило до поминутного графика подачи электроэнергии в цеха завода) – на таком фоне приходилось трудиться нашим литейщикам и кузнецам. И что самое удивительно – добиваться неплохих результатов.
Этапы. 1990 – 2000 г.г.
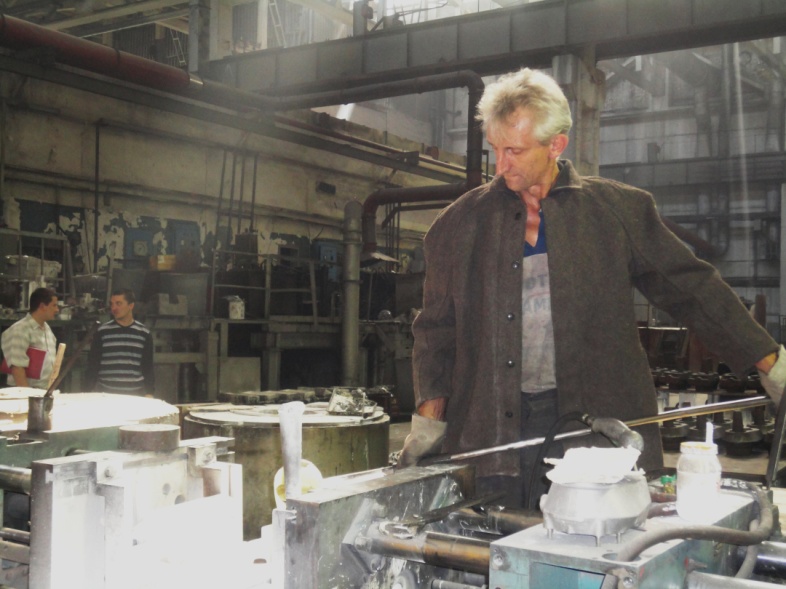
О работе литейщиков в 1992 году генеральный директор завода
Ю.А.Лейковский
сказал следующее: «В этом году мы неплохо подтянули работу ЛШЗ. Прибавка есть и очень существенная. Она по точному литья составила 1,44 раза, сделали 280 тонн вместо 198 тонн. В том числе по гражданской продукции рост в 10 раз. По цветному литью выпуск увеличился в 2,14 раза, стало 458 тонн против 214 тонн в 1991 году. Литейное производство обеспечивает двигатель ДМ-1Д и блоком цилиндра, и головкой цилиндра, и поршнем, и шатуном». В этот период на ЛШЗ также были освоены 3 отливки на карбюратор мотоблока. В 1992 году для участка цветного литья были приобретены две машины для литья под давлением.
Самые трудные годы реформ пережил вместе с цехом литейщик участка цветного литья Н.Н.Полойников. 23 года отдано литейному делу
Работа над конверсионными программами в части мощного развития мотоблочной тематики и освоения производства дизельных и карбюраторных моторов для средств малой механизации не должна была заслонять главную тему калужских моторостроителей – газотурбинную. В период 90-х годов ее приходилось не то чтобы развивать, а спасать. От былых объемов по танковому ГТД остались буквально слезы. Если в 1990 году литейщики обеспечивали в месяц до 120 комплектов литья изд. 029, то к концу 90-х годов объемы упали до 20 комплектов в год. Шел активный поиск альтернативных вариантов развития уникальных газотурбинных направлений. Выше мы уже упоминали о разработанных заводом в этот период газотурбинных комплексах для разрыва нефтяных пластов при извлечении остаточных нефтяных запасов.
Этапы. 1990 – 2000 г.г.
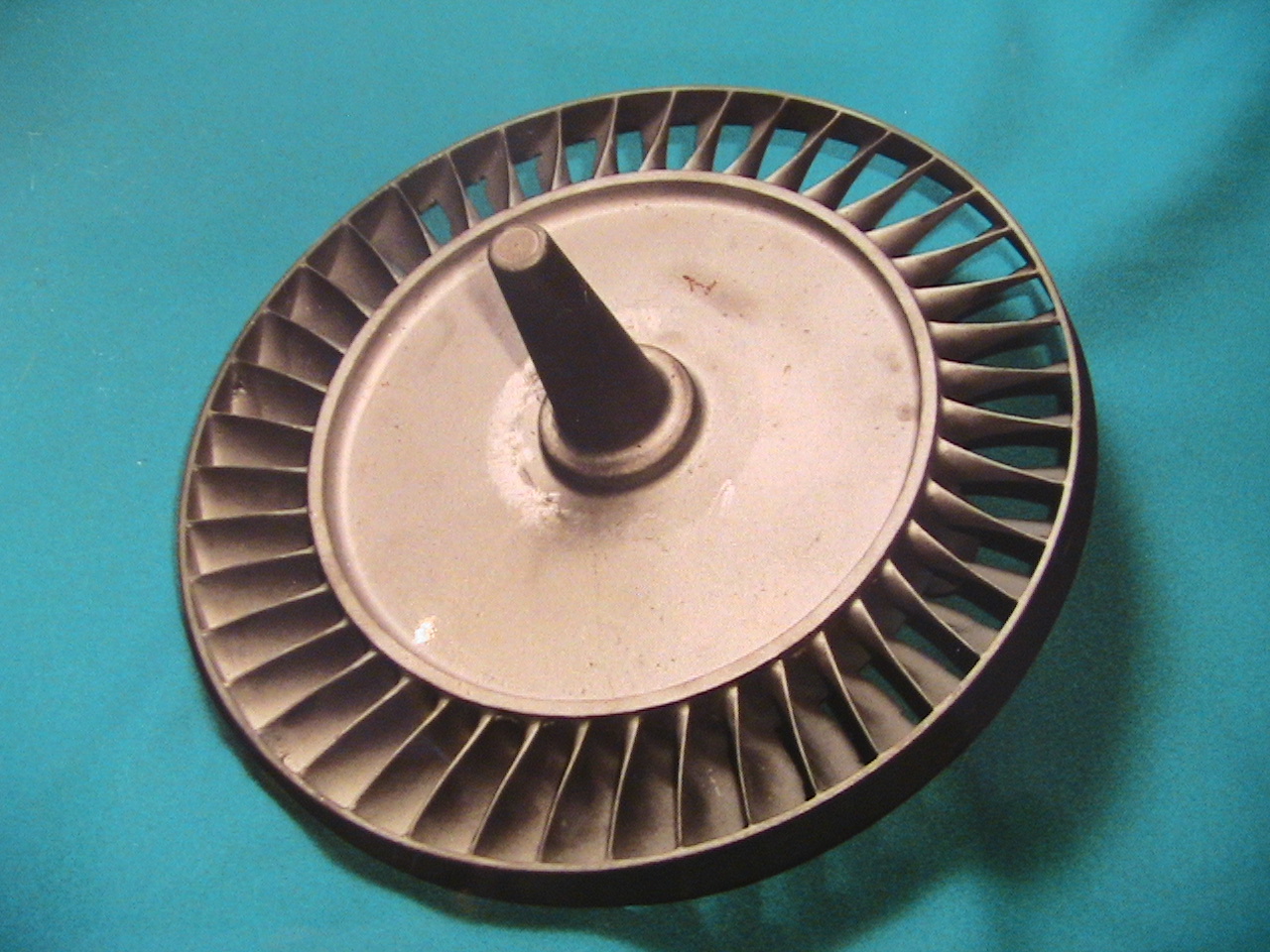
Вскоре литейщики завода получили еще один шанс продемонстрировать свои навыки в изготовлении высокоточных жеропрочных отливок. На этот раз – для разработанных конструкторами КОБМ по заказу Ирана газотурбинных установок. Здесь встал вопрос о технологии вакуумного литья самой, пожалуй, ответственной детали – ротора турбины из жаропрочного сплава ЖС6К-ВИ. Вес отливки достигал 32 кг, что для вакуумной печи УППФ-3М было практически пределом возможностей. В цельном исполнении такого рода отливки до этого не изготавливались, а, как правило, набирались из отдельных, ранее отлитых лопаток. Технологи завода предложили лить ротор целиком. Следовательно – и изготавливать его восковую модель в сборе. Понятно, что цельнолитая технология предъявляла особые требования по точности литья. Ведь, скажем, в обычном варианте сборки роторов, если попадается бракованная лопатка, то ее быстро заменяют годной. В новом же варианте из-за малейшего брачка хотя бы одной из 42 лопаток ротора приходилось забраковывать все изделие целиком. По цене, кстати, приближающееся к стоимости хорошего автомобиля. Стоить ли говорить о том, какой
уровень литейной технологии должен быть для изготовления такого рода изделий.
Награды
Орден «Трудовой Славы» III степени – А.В.Яшин – кузнец-штамповщик (1986 г.)
«Заслуженный моторостроитель» – А.П.Шумилова – начальник ТБ (1996)
«Заслуженный моторостроитель» – В.В.Яшин – электромонтер (1996)
Изготовление иранских роторов – серьезный экзамен для литейщиков
Следующий этап развития литейно-кузнечного направления и завода в целом был обусловлен общим подъемом экономики страны. ЛШЗ вышел из кризиса 90-х вполне работоспособным подразделением. Правда, о былых объемах гособоронзаказа по тому же танковому направлению говорить не приходилось. Объемы упали в разы. Но главное – литейщикам удалось сохранить уникальные технологии по всей газотурбинной тематике. Постепенно осваивались новые изделия, внедрялось современное прогрессивное оборудование. Литейно-кузнечное направление обретало второе дыхание.
Этапы. 2000 – 2011 г.г.
Зам.главного металлурга ОАО «КаДви» С.И.Малышев, работавший ранее директором ЛШЗ, так охарактеризовал первый восстановительный этап развития литейно-кузнечного направления:
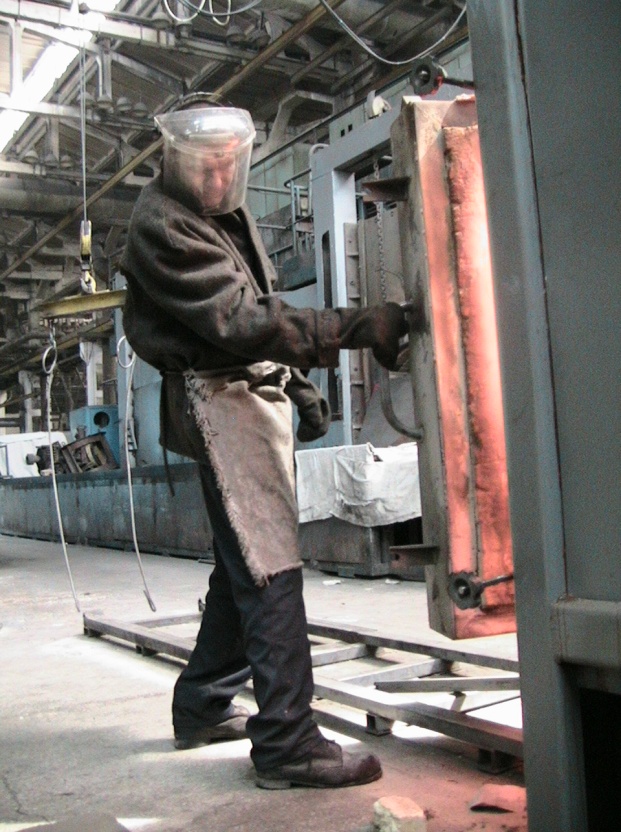
«За 1998-2005 гг. по цеху точного литья была выполнена следующая работа. Отремонтированы и запущены в работу: – 4 пресса для изготовления моделей, установка 6А50 для механизированного изготовления элементов литниково-питающих систем, установка для вытопки модельной массы. Произведена полная реконструкция участка отделения керамики, обрезки и зачистки отливок. Произведен капитально-восстановительный ремонт вакуумной плавильно-заливочной установки УППФ 3М. Приобретено, установлено и запущено в эксплуатацию новое оборудование: установка выгонки модельной массы, плавильная печь ИСТ 04, прокалочная печь с выкатным полом, установка для отделения керамики УВИГ, дробемет, 3 галтовочных барабана.
Освоено более 40 отливок новых наименований, в том числе 8 уникальных: крыльчатка первого каскада изделия 029, цельнолитые ротора и сопловые аппараты из сплавов ЖС6К, 5 наименований крыльчаток из сплава «Нирезист». Внедрены прогрессивные литейные материалы, позволяющие поднять выход годного на 30-40%: пенокерамические фильтры жидкого металла, покрытия моделей на
У прокалочной печи ПВП-3
Этапы. 2000 – 2011 г.г.
основе кварца, новые футеровочные материалы. Внедрено отделение керамики на установке УВИГ вместо ручной отбивки. В целом объемы производства по цеху точного литья выросли по сравнению с 1998 годом в 6 раз. Цех точного литья производит продукцию не только для нужд завода. 40% объемов приходится на заказы сторонних предприятий и организаций, в том числе КЗТА, КОБМ, ЗАО «Страж», ЗАО «Сплав» г.Великий Новгород, ЗАО «Литейные заводы» г.Москва, ЗАО «Твест» г.Москва и др.
Этапы. 2000 – 2011 г.г.
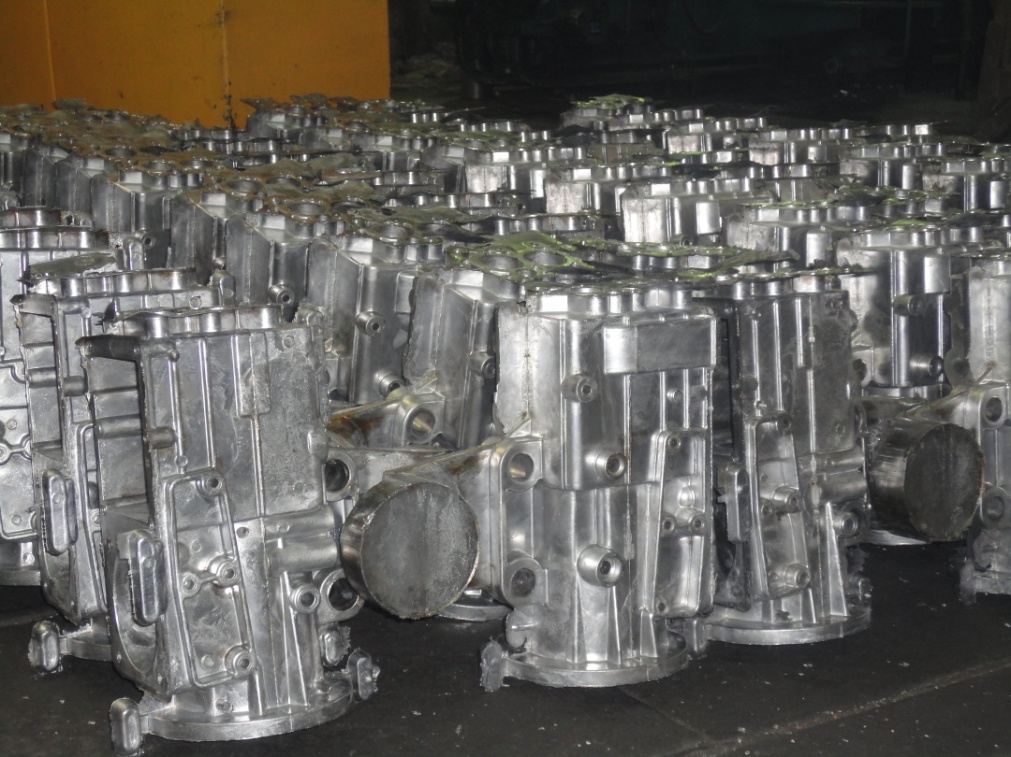
По цеху цветного литья в период с 1998 по 2005 гг. была выполнена следующая работа. Увеличены в 2 раза мощности по участку литья под давлением за счет приобретения и запуска в эксплуатацию трех машин ЛПД мод.1А07 и одной машины 1А09. Восстановлены и запущены в эксплуатацию 2 комплекса кокильных машин, 1 установка АЛУГ-1, и 2 установки АЛУГ-34.
В это время был создан участок чугунного литья с комплексом оборудования: плавильная печь ИСТ 04, две формовочные машины, свешивающие бегуны. Освоено 8 наименований чугунного литья, в том числе осуществлен перевод отливок изд. МБ-90, ранее изготавливаемых из алюминиевых сплавов.
Освоена новая технология – литье в оболочковые формы, для чего приобретены и внедрены в эксплуатацию 2 плавильные установки ИСТ 04, 2 установки изготовления оболочковых форм, 2 линии формовки и заливки деталей, плазменная установка резки прибылей. Был проведен газ и изготовлен стенд для разогрева ковшей. Восстановлен и запущен дробемет.