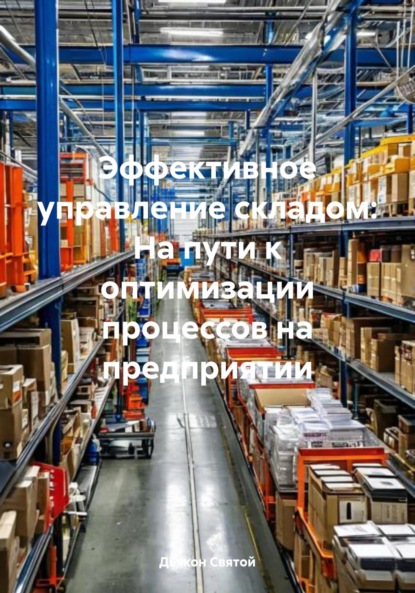
Полная версия:
Эффективное управление складом: На пути к оптимизации процессов на предприятии

Дьякон Святой
Эффективное управление складом: На пути к оптимизации процессов на предприятии
Глава 1. Введение
Управление складом – это один из самых критически важных аспектов производственного процесса, который часто остается в тени. На первый взгляд, склад может показаться простым местом хранения комплектующих, однако он играет ключевую роль в функционировании всей производственной цепочки. Как показывает практика, даже малейшие ошибки в работе склада могут привести к катастрофическим последствиям: от задержек в производственном процессе до значительных финансовых потерь. Буквально одна неправильно отгруженная деталь может остановить сборку ЧПУ станка, и предприятие окажется перед угрозой срыва сроков.
Представим ситуацию на примере компании, занимающейся производством ЧПУ станков. На складе данной компании работали три человека, которые отвечали за приемку комплектующих. Каждый день на склад поступали различные детали: каретки, шпиндели, электродвигатели и прочие важные компоненты. Из-за отсутствия четкой системы учета и хаотичной структуры складирования, работникам приходилось применять экспертное мнение, чтобы быстро находить нужные детали. Часто возникали ситуации, когда комплектующие, имеющие схожие названия и прямые назначения, путались. Например, каретки для одной модели станка часто переставлялись с каретками другой модификации, что вызывало путаницу, когда дело доходило до заказа или отгрузки.
Каждый раз, когда возникали ошибки, команда сборки вынуждена была проводить много часов, чтобы исправить ситуацию, определяя, какая деталь была неправильно отгружена. Это привело не только к задержкам в производстве, но и к снижению морального духа сотрудников, когда они понимали, что хороший результат их труда может быть скомпрометирован неэффективной работой склада.
Попробуем представить, как можно было бы оптимизировать процессы на складе компании. Основная цель – ускорить и упростить работу с комплектующими. Первый шаг к улучшению ситуации заключался в автоматизации учета запасов с помощью системы управления складом (WMS). Внедрив автоматизированную систему, предприятие смогло бы обеспечить фиксирование всех перемещений комплектующих в режиме реального времени, минимизируя человеческий фактор и вероятность ошибок.
На практике это работает следующим образом: каждое комплектующее, поступающее на склад, получает уникальный штрих-код. При приемке этот код сканируется в системе, автоматическое программное обеспечение обновляет инвентарный учет, и информация отображается на экране рабочего места. Теперь работникам больше не нужно запоминать наименования и искать детали методом проб и ошибок. Все данные о доступных комплектующих, их количестве и местоположении находятся в одном месте – в системе, доступной каждому работнику склада.
Кроме автоматизации учета, внедрение стандартов наименования комплектующих стало еще одним важным шагом к сокращению путаницы. В компании был разработан каталог с четкими и понятными описаниями каждой детали, адаптированный под особенности продукционного процесса. Это позволило всем рабочим на складе и в сборочной зоне использовать единые термины, что исключило возможность путаницы. Например, в каталоге наряду с названиями было указано, для каких моделей предназначена каждая деталь. Так, при обращении к названию более не возникало вопросов, какая именно каретка нужна, и ошибки свелись к минимуму.
Для повышения эффективности удалось также оптимизировать процессы приемки и выдачи комплектующих. Каждый сотрудник, принимая или выдавая детали, следовал четким процедурам, фиксируя каждое действие в системе. В случае ошибок или несоответствий, система автоматически уведомляла ответственных, что обеспечивало мгновенное реагирование на возникающие проблемы и дальнейшую их профилактику.
Также немало важным было внедрение визуальных указателей на складе. За счет цветовой кодировки и четких знаков каждый работник сразу мог определить, в какое место отправляться за необходимыми комплектующими. Такие визуальные метки не только ускорили поиск, но и позволили вновь начать работать по отлаженной системе без ненужных задержек и разногласий.
Регулярные инвентаризации стали нормой на этом предприятии. Вместо разовых проверок запасов, которые выполнялись в хаотичном порядке, на складе начали проводиться стандартные ежемесячные инвентаризации. Система самостоятельно оповещала, какие детали не хватает или где наблюдаются избытки, что помогало избегать ситуаций с дефицитом или переизбытком товаров.
Таким образом, через примеры и практические советы, изложенные в этой книге, можно увидеть, как правильно организованное управление складом может значительно повысить уровень эффективности производства. Улучшение процессов работы – ключ к успеху, и такие предприятия, как наш пример, могут извлечь уроки для своей работы и снизить вероятность возникновения ошибок и задержек. В следующих главах мы глубже рассмотрим каждую из предложенных стратегий, их внедрение и влияние на производственный процесс.
5032 из 16384
Беседа № 15:
Выбрана роль: Писатель
Глава 2. Проблемы организации работы склада
Управление складом является важным аспектом в производственном процессе, и его неэффективность может вызвать серьезные проблемы. Чтобы понять, как сложная система складирования может повлиять на общее качество и скорость выполнения заказов, рассмотрим более подробно основные проблемы, с которыми может сталкиваться предприятие.
Представим, что мы возвращаемся на склад той же компании, занимающейся производством ЧПУ станков. Несколько месяцев назад здесь были внедрены некоторые новые процедуры, но недостатки в организации оставались, и с их устранением нужно было работать. Как и в случае с любым процессом, понимание основных проблем является первым шагом на пути к улучшению.
Одной из самых распространенных проблем является путаница на складе из-за отсутствия системы хранения. На складе компании как-то складывались детали, не имея четкой структуры. Без ясного планирования, где и как размещать комплектующие, рабочие могли часами искать необходимые детали. Например, однажды работник, отвечающий за сборку, запросил комплектующие для конкретного станка, но вместо шпинделей для модели X на складе оказались шпиндели для модели Y. Из-за отсутствия единообразия в размещении, у работников возникали сложности, так как они просто не знали, какие детали где находятся.
Этот хаос не только замедлял процесс сборки, но также ухудшал моральный климат в команде. Работники начали терять доверие друг к другу, и заявления о том, что кто-то неправильно разместил детали, становились частыми. Это создавало напряжение в коллективе, ведь каждый считал себя виноватым за возникшие трудности.
Еще одной серьезной проблемой стали временные задержки, связанные с приемкой и отгрузкой комплектующих. Когда на склад поступали новые партии деталей, осуществить их проверку по количеству и качеству не всегда удавалось. Это происходило из-за недостатка рабочей силы и протоколов для приемки. В результате некоторые комплектующие не были ограждены от повреждений или не соответствовали заявленным стандартам, создавая дополнительную нагрузку на сборку. Возникал замкнутый круг: некоторые плановые сборки не удавались, и загруженность команды сборщиков увеличивалась, а необходимость в исправлении конструктивных ошибок вызывала ещё большее недовольство.
В случае с нашей компанией, проблемы становились еще более усугубленными из-за отсутствия более узкой специализации среди работников. Все сотрудники выполняли несколько ролей, что приводило к путанице и ошибкам. Например, один и тот же работник мог заниматься и приемкой, и выдачей комплектующих, и даже упаковкой готовой продукции. Это создавало накладные расходы и требовало времени, которое могло быть использовано более эффективно. В итоге, эти задержки приводили к срыву сроков выполнения заказов клиентами.
Чтобы понять, каковы были причины этих проблем, нужно вспомнить об условиях работы на складе. На складе не проводилось регулярного обучения для сотрудников по работе с нововведениями в сфере приемки, хранения и выдачи. Кроме того, дважды в год выполнялись инвентаризации, но их результаты оставались непереработанными, и анализ не велся. Отчетность по ошибкам не передавалась между сменами, и любой сотрудник оставался в неведении о проблемах, с которыми столкнулись его коллеги. Поэтому ошибки повторялись и создавали накопления ситуаций, требующих внимания.
Таким образом, для лучшего управления поставками и складом необходимо было не только устранить текущие недостатки, но и привести в порядок общую организацию работы. Прежде всего, требовалось установить четкие процессы по размещению, учету и возврату комплектующих.
Первая успешная мера состояла в внедрении стандартов для хранения комплектующих. Введя систему зонирования на складе, предприятие определило, какие категории комплектующих должны располагаться в определенных местах. Каждый тип детали получил свою зону с четкими границами и знаками, облегчая доступ к ним. Например, шпиндели размещались в одной зоне на полках, маркированных названием изделий и их артикулами, что исключало вероятность их смешивания с другими комплектующими.
Вторым шагом стало объединение процессов приемки и выдачи комплектующих под одной крышей с четким учетом каждой операции. Для этого упрощённые инструкции были предоставлены всем сотрудникам, чтобы они могли эффективно выполнять свою работу. Обучение стало постоянным процессом, и к каждому новому этапу адаптировались уже имеющиеся кадры. К примеру, работа с комплексной системой учета образовала группу сотрудников, обладающих необходимыми навыками для быстрого реагирования на ситуации, когда возникали ошибки или задержки.
Во избежание временных задержек и предупреждения несоответствий в качестве проводились регулярные проверки. Каждая поставка проходила обязательный контроль по количеству и качеству, и только после его завершения комплектующие принимались на склад. Таким образом, дисциплина и ответственность были выставлены в приоритет.
Не менее важной частью нового подхода стало создание специального рабочего времени для проведения инвентаризаций. Вместо того чтобы проводить их раз в полгода, введение ежемесячных проверок помогло бы регулярно обновлять данные о запасах и выявлять любые несоответствия. Поскольку все проблемы были четко фиксированы и анализировались, стало намного проще предотвращать их повторение.
Итак, в этой главе мы рассмотрели основные проблемы, с которыми сталкиваются склады, и проиллюстрировали, как, понимая их суть, можно вводить эффективные изменения. Проблемы, возникшие на складе нашей компании, сигнализировали о более глубоком кризисе в организации работы, и успешное управление этими процессами требует четкой структуры, прозрачности и стабильности. Это, в свою очередь, повысит эффективность управления складом и сделает его истиной опорой для производственного процесса. В следующих главах мы углубимся в методы автоматизации работы склада, чтобы далее повысить качество и скорость выполняемых функций.
7079 из 16384
Беседа № 15:
Выбрана роль: Писатель
Глава 3. Автоматизация учета на складе
автоматизация учета на складе является одним из наиболее важных шагов, которые могут быть предприняты для повышения эффективности операций и снижения вероятности ошибок. В современном мире, когда скорость и точность имеют решающее значение, принципы классического учета запасов перестают соответствовать требованиям высокопроизводительных предприятий. Рассмотрим, как интеграция автоматизированной системы управления складом (WMS) помогла исправить ситуацию на примере той же компании, занимающейся производством ЧПУ станков.
Перед внедрением роботизированной системы учета, работники на складе использовали исключительно бумажные документы и ручные записи. Каждый день сотрудники были вынуждены заполнять журналы о приходе и расходе комплектующих, что требовало много времени и часто приводило к ошибкам. Например, представьте себе ситуацию, когда на склад поступали новые каретки для станков, и один из работников по ошибке записал количество в журнале как 150 единиц вместо 120. Эта ошибка не только привела к неправильному учету, но и вызвала заторы при отгрузке, поскольку на момент подготовки заказа оказалось, что правильное количество комплектующих уже было распродано.
Однако это была лишь часть беды. Множество ручных записей требовало постоянного обновления. Работники часто забывали фиксировать внутренние перемещения, что приводило к путанице в запасах. Это стало причиной серьезных недостатков, когда заказы не могли быть выполнены вовремя из-за нехватки необходимых комплектующих. Вместо того чтобы сосредоточиться на сборочном процессе, команда оказалась вовлечена в бесконечные поиски и разборки.
Ситуация изменилась, когда компания приняла решение внедрить автоматизированную систему учета. Здесь важно понимать, что такая система не заменяет работников, а, наоборот, освобождает их от рутинной бумажной работы, позволяя сосредоточиться на более важных задачах. Автоматизированная система управления складом (WMS) использует современные технологии для отслеживания и управления движением запасов в реальном времени.
Процесс внедрения системы начался с анализа потребностей предприятия и выбора подходящего программного обеспечения. Важно было учитывать особенности работы склада, такие как виды комплектующих, объём операций и численность персонала. После завершения оценки и выбора программного обеспечения началась интеграция WMS с имеющейся системой ERP (Enterprise Resource Planning), что позволило обеспечить бесшовный поток информации из разных направлений.
Когда система была внедрена, каждое комплектующее, поступающее на склад, получило уникальный штрих-код. Работники теперь использовали сканеры для считывания информации о комплектующих. Система автоматически обновляла инвентарный учет, фиксируя все перемещения и оставляя все данные доступными для быстрого поиска. Например, когда на склад поступали новые каретки, работник просто сканировал код на упаковке, и информация о деталях мигом обновлялась в WMS, а каждое новое поступление автоматически фиксировалось в системе.
Этот процесс не только уменьшил вероятность ошибок при учете, но и улучшил видимость запасов на складе. Теперь работники могли с легкостью отслеживать, сколько комплектующих доступно в любой момент. Более того, когда возникал срочный заказ на конкретные детали, работники в считанные минуты могли получить актуальные данные о наличии и местоположении этих запасов.
Важным аспектом автоматизации стало и улучшение процедуры отгрузки. Работники теперь могли с помощью системы легко проверить наличие всех необходимых комплектующих перед подготовкой заказа. Как только задание было подтверждено, система автоматически генерировала список комплектующих, которые нужно было отгрузить, а работники просто следовали этому списку, проверяя наличие деталей в реальном времени. Это значительно ускоряло весь процесс, минимизируя время, затрачиваемое на тщательные проверки и поиски.
Автоматизация также привела к повышению уровня ответственности среди работников. Каждый сотрудник теперь знал, что его действия фиксируются в системе, и в случае возникновения ошибок они могут быть легко отслежены и проанализированы. Эта прозрачность укрепила доверие внутри команды и способствовала повышению общей производительности.
Кроме того, внедрение WMS открыло двери к более сложным аналитическим инструментам. Теперь руководство могло проводить анализ движения запасов, понимание, какие комплектующие добирались до точки продаж быстрее, а какие оставались на складе слишком долго. Эти данные позволяли более точно планировать закупки и определять оптимальный уровень запасов для обеспечения бесперебойного производства без излишних затрат на хранение.
В дополнение к этому, использование системы позволяло оперативно планировать и проводить инвентаризации. Учитывая, что вся информация хранилась в единой базе данных, данные о количестве и состоянии запасов всегда были актуальными. Система могла автоматически генерировать отчёты об излишках или дефиците любых комплектующих, что обеспечивало своевременную реакцию на возможные проблемы.
Хотя внедрение автоматизированной системы управления складом требовало определенных затрат на обучение персонала и техническую поддержку, конечный результат очевидно превзошёл ожидания. Компании удалось значительно улучшить уровень обработки заказов, уменьшить количество ошибок и, как следствие, повысить качество обслуживания клиентов.
Таким образом, автоматизация учета на складе кардинально изменила условия работы и уровень выпускаемой продукции на компании. Неэффективные процессы были заменены более современными и надежными решениями, что дало возможность сосредоточиться на основном бизнесе – производстве качественных ЧПУ станков. В последующих главах мы продолжим исследовать другие аспекты управления складом, такие как использование штрих-кодов и QR-кодов, а также стандартизацию операций, которые помогут ещё больше повысить эффективность и снижать расходы.
Использование штрих-кодов и QR-кодов
Внедрение штрих-кодов и QR-кодов на складе является важным шагом на пути к модернизации управления запасами и оптимизации процессов. Эти технологии позволяют значительно повысить скорость и точность операций, уменьшая вероятность ошибок, связанных с ручным вводом данных. Рассмотрим это на примере компании, производящей ЧПУ станки, которая успешно интегрировала данные технологии в свою деятельность.
Прежде чем перейти к реализации системы, компания столкнулась с рядом проблем в управлении запасами. На складе работали несколько сотрудников, которые обеспечивали приемку, обработку и выдачу комплектующих. Каждый день на склад приходило множество заказов, и процесс обработки документов зачастую вызывал заторы. Работники вынуждены были тратить много времени на поиск необходимых комплектующих, что замедляло весь производственный процесс. Более того, отсутствие четкой структуры учета приводило к путанице в наименованиях деталей, что также способствовало ошибкам и недоразумениям.
Ситуация кардинально изменилась после того, как команда приняла решение внедрить систему штрих-кодов. Первая задача заключалась в том, чтобы создать уникальную идентификацию для каждой детали, поступающей на склад. Для этого было решено использовать стандартные штрих-коды, что позволяло легко их считывать с помощью сканеров, подключенных к системе управления складом (WMS).
Специалисты компании совместно с программистами разработали программу, которая генерировала и распечатывала штрих-коды для новых поступлений. Каждая деталь на складе, включая каретки, шпиндели и электродвигатели, получила свой уникальный код, который содержал информацию о наименовании, количестве, сроках поставок и даже о месте хранения. Таким образом, каждый комплектующий не только имел свой физический идентификатор, но и был связан с его данными в системе управления запасами.
Когда процесс внедрения завершился, сотрудники получили современные сканеры, которые можно было использовать для быстрого считывания информации при приемке и выдаче комплектующих. Теперь работники могли просто сканировать штрих-код на упаковке, и система автоматически обновляла инвентарный учет, фиксируя все перемещения. Этот процесс существенно сократил время, необходимое для выполнения рутинных операций. Например, при поступлении новой партии кареток, сотрудники могли в считанные минуты закончить приемку, не вводя данные вручную.
Конец ознакомительного фрагмента.
Текст предоставлен ООО «Литрес».
Прочитайте эту книгу целиком, купив полную легальную версию на Литрес.
Безопасно оплатить книгу можно банковской картой Visa, MasterCard, Maestro, со счета мобильного телефона, с платежного терминала, в салоне МТС или Связной, через PayPal, WebMoney, Яндекс.Деньги, QIWI Кошелек, бонусными картами или другим удобным Вам способом.
Вы ознакомились с фрагментом книги.
Для бесплатного чтения открыта только часть текста.
Приобретайте полный текст книги у нашего партнера:
Полная версия книги
Всего 10 форматов